Precision in Your Cup: How Coffee Grind Size Mirrors CNC Machining Tolerances?
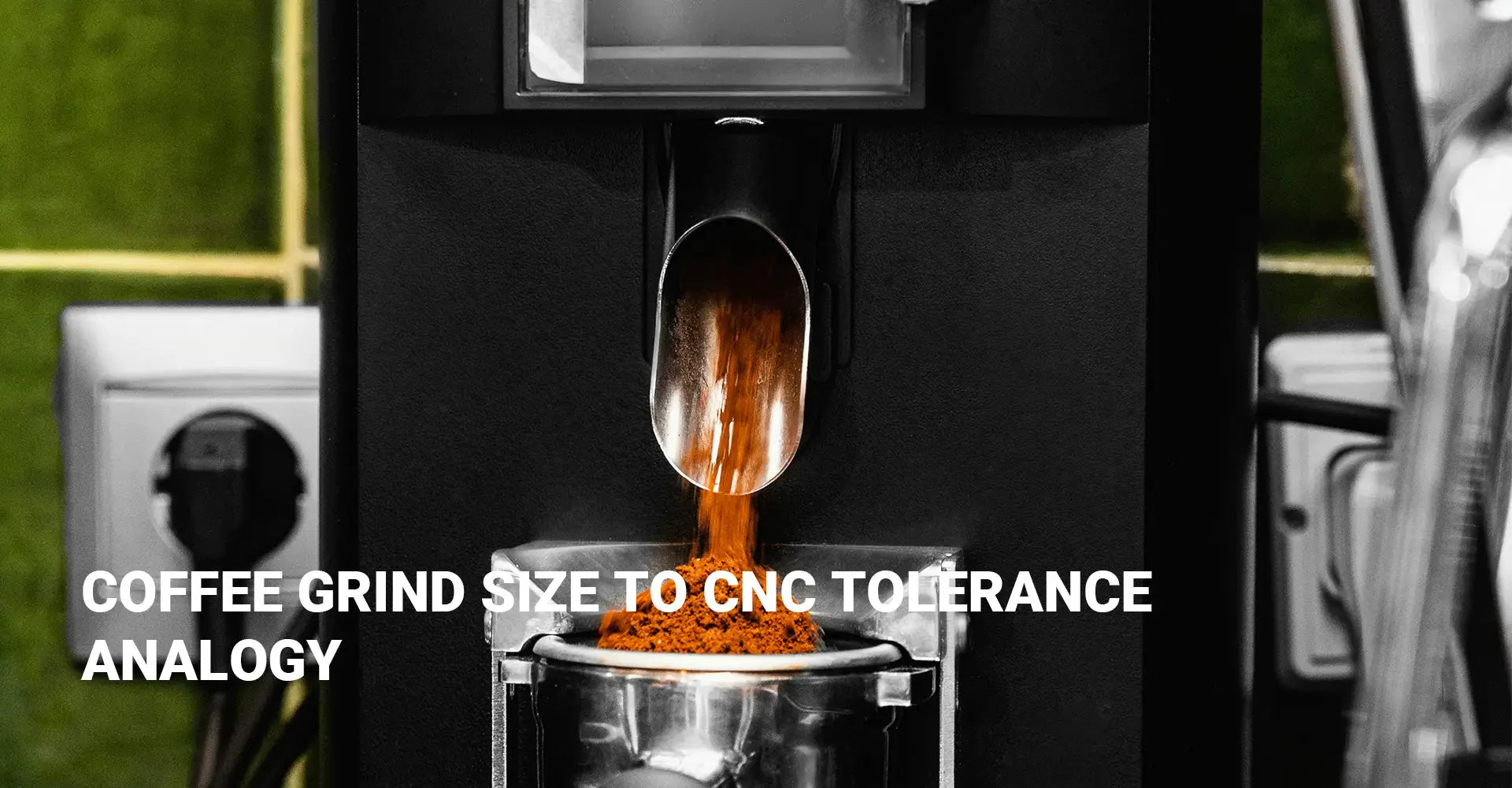
Precision in Your Cup: How Coffee Grind Size Mirrors CNC Machining Tolerances?

Your morning espresso and a precisely machined aerospace component share more in common than you might think. Both rely on exacting standards of measurement and consistency that determine success or failure. This unexpected connection between the art of coffee brewing and the science of CNC machining reveals fascinating parallels that can deepen your understanding of both worlds.
When baristas obsess over achieving the perfect 250μm coffee particle for espresso extraction, they're unconsciously working within the same framework of precision that engineers use when specifying ±0.05mm tolerances for critical components. In both fields, micron-level consistency determines quality outcomes. The difference between a bitter cup of coffee and a perfectly balanced one mirrors the gap between a machined part that fits flawlessly and one that fails quality inspection.
Exploring these surprising connections between specialty coffee and precision manufacturing offers valuable insights for professionals in both industries. By understanding how particle distribution affects extraction in coffee, engineers can better explain complex tolerance concepts to clients and stakeholders. Likewise, coffee professionals can leverage engineering principles to achieve more consistent brewing results. These cross-disciplinary insights transform technical concepts into practical knowledge that improves outcomes in both fields.
[Table Of Content]
- From French Press to IT7: Can Coffee Particles Explain CNC Precision Standards?
- The Channeling Effect: Why Do Coffee Extraction Problems Resemble CNC Surface Defects?
- Brewing Profitability: What Does Your Coffee Budget Teach About Manufacturing Costs?
- Measuring Success: How Do Coffee Professionals and Engineers Evaluate Quality?
- Conclusion
From French Press to IT7: Can Coffee Particles Explain CNC Precision Standards?
The difference between coffee brewing methods comes down to precise particle sizes that determine extraction rates. When a barista adjusts their grinder from coarse to fine, they're working within measurement parameters remarkably similar to ISO tolerance grades used in precision machining. The 800μm particles ideal for French press brewing correspond roughly to IT12 tolerance grades (±0.25mm), while the 250μm particles needed for espresso parallel IT8 grades (±0.05mm) used in CNC metal machining.
Just as inconsistent coffee grounds lead to uneven extraction and flavor defects, imprecise tolerances in manufacturing cause assembly issues and performance problems. A coffee grinder producing particles with 15% size variance will create noticeably flawed extraction, while a CNC machine operating outside IT8 tolerance specifications will produce components that may fail to fit properly. Both worlds demand consistency for quality results, with tighter specifications required for more demanding applications.
The Specialty Coffee Association establishes specific particle size ranges for different brewing methods, mirroring how engineering standards define acceptable tolerance ranges for various applications. Turkish coffee's ultra-fine 100μm particles correspond closely to the stringent IT6 tolerance grade (±0.01mm) required for aerospace components. Both fields rely on statistical distribution measurements rather than simple averages, using terms like "D50" (median particle size) in coffee that parallel "nominal dimension" in machining. This shared language of precision creates a framework for quality control across seemingly unrelated disciplines. When specialty coffee equipment manufacturers advertise "precision-engineered grinders," they reference the same principles governing CNC machining tolerance specifications.
The Channeling Effect: Why Do Coffee Extraction Problems Resemble CNC Surface Defects?
When water flows unevenly through a coffee bed, creating channels where it follows paths of least resistance, extraction becomes inconsistent – some grounds over-extract while others remain under-extracted. This "channeling" phenomenon has a direct parallel in manufacturing when machined surfaces have inconsistent finishes that affect fluid flow across mechanical components. In both cases, uneven distribution creates performance problems that diminish quality.
The numbers tell the story: a 15% inconsistency in coffee grind distribution typically leads to a 30% variance in extraction yield, dramatically affecting taste. Similarly, a surface finish roughness of Ra 3.2μm in a CNC-machined hydraulic component can increase leakage risk by 25%. These parallels demonstrate how particle and surface consistency directly impact performance in both coffee brewing and precision manufacturing, with small variances creating significant functional differences.
Coffee extraction and machined surface performance both depend on uniform particle and feature distribution. When coffee grounds contain too many "fines" (extremely small particles), they clog filters and create back pressure, similar to how burrs and microscopic irregularities on machined surfaces create turbulence and pressure drop in fluid systems. Professional baristas use distribution tools to ensure even coffee beds, just as machinists employ surface finishing techniques to eliminate irregularities. These parallel approaches solve similar problems: achieving consistent interaction between a medium (water or hydraulic fluid) and a precisely prepared surface. Understanding these similarities helps professionals in both fields identify and resolve consistency issues more effectively.
Brewing Profitability: What Does Your Coffee Budget Teach About Manufacturing Costs?
The economics of precision apply equally to coffee shops and manufacturing facilities. Over-engineered solutions in both fields often waste resources without providing proportional quality improvements. A specialty coffee shop investing in ultra-consistent grinding capabilities might experience diminishing returns, just as a manufacturer specifying unnecessarily tight tolerances for CNC machined parts faces exponentially higher production costs without meaningful performance benefits.
Consider this revealing comparison: requiring an IT6 tolerance (±0.01mm) when IT8 (±0.05mm) would suffice nearly doubles manufacturing costs - from $0.18 per cubic centimeter to $0.35. Similarly, coffee shops pursuing the "perfect" grind beyond customer perception thresholds might spend 40% more on premium grinding equipment without creating flavor improvements that customers can actually taste. In both industries, finding the optimal precision level represents a critical business decision.
Finding the optimal precision "sweet spot" represents the key to profitability in both coffee and manufacturing businesses. Coffee roasters have discovered that while consistency matters tremendously between 200-500μm particles, pursuing tighter distributions below this threshold yields minimal taste improvements despite requiring significantly more expensive equipment. Likewise, manufacturing engineers know that specifying IT8 tolerance for non-critical dimensions of metal and plastic parts instead of IT6 can maintain functional integrity while reducing machining time by 35% and tooling costs by 25%. This balanced approach to precision represents mature understanding in both fields - knowing exactly where precision matters most and where additional refinement delivers diminishing returns. By analyzing the true requirements of each application, professionals in both industries can optimize the cost-quality equation.
Measuring Success: How Do Coffee Professionals and Engineers Evaluate Quality?
Professional baristas and manufacturing engineers share an obsession with measurement tools that reveal what the human eye cannot see. The coffee refractometer measuring Total Dissolved Solids (TDS) serves the same fundamental purpose as a surface roughness tester in manufacturing - quantifying quality factors that extend beyond visual inspection. Both tools transform subjective experiences into objective measurements that guide process improvements.
Coffee professionals use specialized tools like sieve analyzers that separate particles by size into statistical distributions - reporting D10, D50, and D90 values that indicate the percentage of particles below specific sizes. Engineering quality control for CNC machined products employs remarkably similar statistical approaches, using coordinate measuring machines (CMMs) to generate histograms showing dimensional variation across production lots. These measurement methodologies allow both industries to maintain consistency across time and between different production runs.

Both industries ultimately rely on objective measurement to validate subjective quality perceptions. While a coffee customer experiences "smoothness" or "bitterness," these sensory experiences correlate with measurable extraction percentages (18-22% being ideal). Similarly, a machine operator might subjectively note that parts "fit together well," but this experience correlates with specific measurable surface finish and tolerance achievements. The ability to connect sensory outcomes with quantifiable parameters represents mastery in both fields. This parallel extends to certification standards, with the Specialty Coffee Association (SCA) establishing brewing control charts much like ISO standards establish acceptable tolerance ranges for CNC machined components - both creating frameworks that transform subjective quality assessments into measurable targets that guide repeatable success.
Conclusion
The fascinating parallels between coffee grinding precision and CNC machining tolerances reveal universal principles of quality control that transcend industry boundaries. Both domains demonstrate that consistency at the microscopic level, precise measurement capabilities, and finding the optimal balance between cost and quality lead to superior outcomes. These connections offer valuable insights for professionals seeking to improve their understanding of precision requirements in either field.
Whether you're pursuing the perfect espresso extraction or manufacturing aerospace-grade components, the underlying science of particle size distribution and tolerance management follows remarkably similar patterns. By recognizing these connections, professionals in both fields can better communicate technical concepts and develop more effective approaches to quality control and process optimization.
External Links Recommendation
[Specialty Coffee Association Brewing Fundamentals][^1]
[Coffee Science Foundation Research on Particle Distribution][^2]
[ISO 2768 General Tolerances for Linear Dimensions Documentation][^3]
---
[^1]: Explore this resource to understand the essential brewing techniques and standards set by the Specialty Coffee Association, enhancing your coffee-making skills.
[^2]: Delve into this research to learn how particle distribution affects coffee extraction and flavor, crucial for any coffee enthusiast.
[^3]: Understanding ISO 2768 is vital for precision in engineering and manufacturing, ensuring quality and consistency in your projects.
-
Posted in
CNC machining