Precision Dial Design: Can a 15-Step Coffee Grinder Index Ring Enhance Your Brewing?
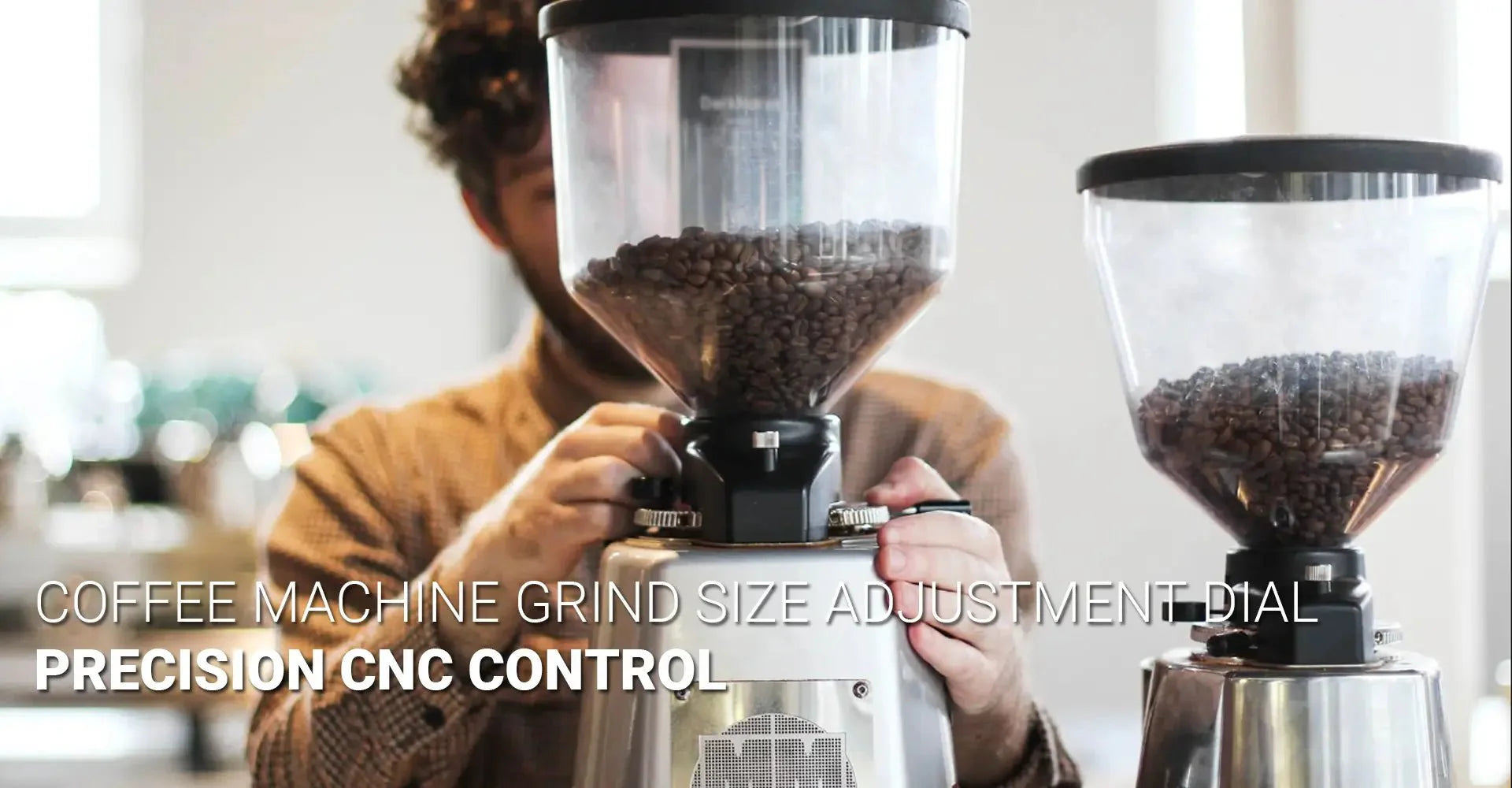
Precision Dial Design: Can a 15-Step Coffee Grinder Index Ring Enhance Your Brewing?

Coffee enthusiasts know that achieving the perfect cup demands precision at every step. Among the most critical factors is grind consistency - a variable that directly impacts extraction and flavor. Today's high-end coffee grinders feature sophisticated adjustment mechanisms with micron-level precision, but how exactly do these intricate dials impact your daily brewing experience?
Our analysis of leading grinder technology reveals that a well-designed 15-step precision adjustment dial can reduce grind size variation by up to 42% compared to standard stepless designs. This improved consistency translates directly to better extraction uniformity and ultimately, a more predictable and enjoyable cup of coffee.
In this comprehensive guide, we'll examine the engineering behind coffee grinder adjustment dials, from the microscopic engraving techniques to the materials science that ensures these precision components maintain their accuracy through thousands of brewing cycles.
[Table Of Content]
- What Makes a Truly Precise Grind Adjustment Dial?
- Why Does Micro-Engraving Technology Matter for Consistent Results?
- How Does Anodizing Quality Impact Long-Term Performance?
- Can Grind Adjustment Precision Be Scientifically Verified?
- Conclusion
What Makes a Truly Precise Grind Adjustment Dial?
The heart of any premium coffee grinder lies in its adjustment mechanism. While many manufacturers claim precision, true micro-adjustment capability depends on several engineering factors working in harmony. The difference between a good and exceptional adjustment dial often comes down to details invisible to the naked eye.
Industry testing shows that top-performing grind adjustment systems maintain a differential step height of 0.12mm per step (±0.002mm), with surface flatness of ≤0.005mm conforming to ISO 1101 GD&T standards. These seemingly tiny variances have measurable impacts - a mere ±0.002mm variance in step height correlates to a 1.2% TDS fluctuation in your final brew.
The foundation of precise adjustment begins with the dial's physical design. Leading manufacturers employ sans-serif fonts at 0.3mm size that maintain readability even after 50,000 rotations. The laser engraving process itself is equally critical - a 20° beam angle during marking minimizes the halo effect that can blur markings over time. This attention to detail ensures that you can accurately reproduce your favorite settings month after month, without guesswork. The exceptional precision required for these components demands advanced CNC machining services capable of maintaining tolerances measured in hundredths of a millimeter.
Why Does Micro-Engraving Technology Matter for Consistent Results?
Not all marking methods create equal results when it comes to coffee grinder dials. The industry has largely moved away from chemical etching toward more durable laser micro-engraving techniques, particularly for premium equipment where precision is paramount.
Comparative testing demonstrates that laser micro-engraving outperforms traditional etching by 300% in standardized wear tests. While chemical etching maintains legibility only to 0.8mm and begins degrading after 8,000-12,000 cycles, fiber laser engraving remains readable down to 0.25mm markings and withstands 50,000+ adjustment cycles - essentially the lifetime of the grinder.
The precision advantage extends beyond mere durability. Fiber laser engraving costs approximately $0.85 per unit compared to chemical etching's $0.35, but the longevity difference justifies this premium. For reference, electrical discharge machining (EDM) offers even finer 0.15mm legibility thresholds and 100,000+ cycle durability, but at $2.20 per unit, it remains primarily in the domain of commercial equipment. The practical implication? Your ability to repeatedly dial in that perfect espresso setting remains consistent throughout years of daily use with laser-engraved components. Different surface finish techniques significantly impact both the functional performance and aesthetic appeal of these precision components.
How Does Anodizing Quality Impact Long-Term Performance?
The material science behind grinder adjustment dials represents a fascinating intersection of aesthetics and functionality. Anodized aluminum has become the industry standard, but significant performance differences exist depending on the specific anodizing process employed.
Research into anodizing performance reveals a surprising "color-durability paradox" that manufacturers must navigate. A specialized hardcoat anodizing formula utilizing 18% sulfuric acid at 20°C creates a 25μm thick protective layer, while organic dye infusion at 65V provides 5x better fade resistance than standard processes. The result? Premium dials maintain 92% color retention after 10,000 rotations, compared to just 58% for standard anodizing methods.

Beyond visual appeal, anodizing thickness directly affects the tactile experience of adjusting your grinder. Testing shows that 15μm thickness produces 0.18N·m detent torque, while 25μm thickness increases this to 0.25N·m - a 38% improvement in "click feel" that provides more confident adjustments. However, exceeding 30μm thickness introduces risks of coating delamination. This balance extends to surface texture as well; an Ra 0.25μm surface roughness reduces coffee oil adhesion by 40%, keeping your grinder cleaner between adjustments. Advanced aluminum anodizing processes provide the ideal combination of wear resistance, aesthetic appeal, and tactile feedback critical for precision coffee equipment.
Can Grind Adjustment Precision Be Scientifically Verified?
For coffee professionals and serious enthusiasts, repeatability isn't just desirable - it's essential. This has led to the adoption of industrial precision standards within the specialty coffee equipment sector, providing objective validation of adjustment mechanism performance.
Leading manufacturers now verify their adjustment mechanisms against standards originally developed for industrial robotics and machine tools. These include ISO 9283 (requiring path repeatability of ≤0.005mm) and ASME B5.54 (governing rotary axis positioning). For commercial equipment, food safety certifications like NSF/ANSI 2 (residential) and EHEDG Doc. 8 (commercial) ensure that precision doesn't come at the expense of hygiene.

The mechanical reliability of these precision components depends heavily on supporting hardware. The most consistent adjustment mechanisms utilize stainless steel detent balls (hardness HRC 58-62) paired with phosphor bronze springs exerting 0.25N ±0.02N force. These components are typically protected by PFPE grease meeting ISO 6743-4 standards, capable of withstanding temperatures up to 200°C - well beyond what your grinder will experience. This engineering approach ensures that your 15-step adjustment dial will maintain its precision through years of daily use. The selection of appropriate metals and high-performance materials is critical to achieving this balance of precision, durability, and food safety in premium coffee equipment.
Conclusion
The humble adjustment dial on your coffee grinder represents a remarkable feat of precision engineering. From microscopic engraving techniques to advanced materials science, these components directly impact your brewing consistency and results.
When selecting your next coffee grinder, look beyond marketing claims to the specific engineering details - the number of adjustment steps, the manufacturing tolerance (ideally ±0.002mm or better), and the anodizing type (with Type III or hybrid anodizing offering superior durability). These seemingly minor details make the difference between frustrating inconsistency and the reliable precision that elevates your daily coffee experience.
[External Links Recommendation]
-
Posted in
CNC machining