How Can You Master End Milling for Superior Machining Results?
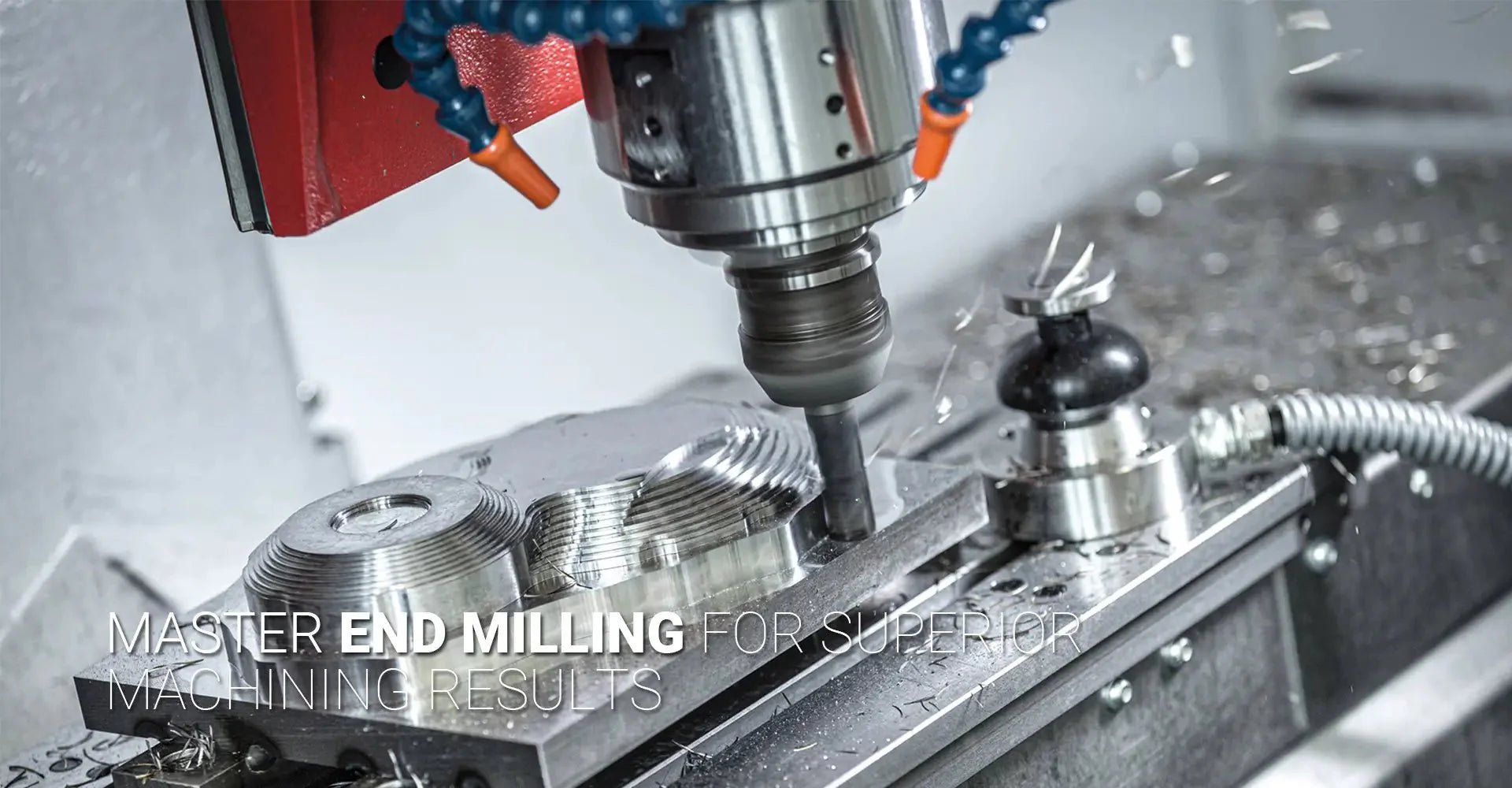
How Can You Master End Milling for Superior Machining Results?

End milling stands as one of the most versatile machining processes in today's manufacturing world. This cutting technique, which uses rotating multi-point cutting tools to remove material, forms the backbone of countless production operations. Whether you're creating complex aerospace components or precision automotive parts, understanding the fundamentals of end milling can dramatically improve your machining outcomes and production efficiency.
Did you know that selecting the right end mill can reduce machining time by up to 40% while extending tool life by 3-5 times? In this comprehensive guide, we'll explore everything from basic end milling concepts to advanced strategies that professional machinists use daily. You'll discover how flute count, helix angles, and material selection directly impact your machining success, along with practical tips for achieving superior surface finishes every time.
Before diving into the technical details, let's clarify what makes end milling distinct from other machining processes and why mastering this technique is crucial for anyone involved in CNC machining, tool design, or manufacturing operations. The following sections will walk you through everything you need to know about end milling processes, from tool selection to application-specific strategies.
[Table of Contents]
- What Makes End Milling Different from Other Cutting Processes?
- How Do Flutes, Helix Angles, and Cutting Edges Impact Your End Milling Success?
- Which End Mill Material Is Best for Your Specific Application?
- What Strategies Can You Implement to Achieve Perfect Surface Finish in End Milling?
- Conclusion
What Makes End Milling Different from Other Cutting Processes?
End milling distinguishes itself through its remarkable versatility and precision capabilities. Unlike turning operations where the workpiece rotates, in end milling, the cutting tool rotates while the workpiece remains stationary or moves along programmed paths. This fundamental difference allows end milling to create complex geometries, slots, pockets, and contoured surfaces that would be impossible with other techniques.
The key distinction between end milling and face milling lies in how the cutting edges engage with the material. End mills cut primarily with their periphery and end face, allowing for both side and plunge cutting operations. Moreover, end milling typically uses smaller diameter tools (2-25mm) compared to face milling cutters, making it ideal for detailed work requiring precision rather than bulk material removal. For complex projects requiring precise end milling operations, custom CNC milling services can provide the expertise and equipment needed to achieve outstanding results.

When examining cutting mechanics, end milling generates forces in multiple directions due to the rotating cutting edges engaging with the workpiece at varying angles. This creates distinct chip formation patterns and cutting forces that machine operators must account for. Additionally, end milling operations can be further classified as conventional milling (cutter rotates against the feed direction) or climb milling (cutter rotates with the feed direction), each offering specific advantages depending on your machine rigidity and surface finish requirements.
How Do Flutes, Helix Angles, and Cutting Edges Impact Your End Milling Success?
The geometry of your end mill directly determines its performance across different materials and applications. Three critical design elements—flute count, helix angle, and cutting edge geometry—form the foundation of end mill performance characteristics. Understanding these parameters helps you make informed decisions when selecting tools for specific jobs.
Flute count significantly affects chip evacuation and cutting efficiency. Two-flute end mills excel in aluminum and non-ferrous materials by providing ample chip clearance, while four-flute designs deliver superior surface finishes in steel. Helix angles ranging from 30°-45° suit general-purpose applications, but angles exceeding 60° dramatically reduce vibration when machining harder materials. Real-world testing shows that a properly selected 45° helix carbide end mill can increase tool life by up to 40% when machining challenging materials like titanium. The proper combination of these elements is essential when working with various CNC metals and plastics, as each material responds differently to cutting forces and heat generation.

Beyond basic geometry, modern end mills incorporate sophisticated features like variable helix designs and unequal flute spacing to disrupt harmonic vibrations that cause chatter. The cutting edge preparation also plays a crucial role—sharp edges cut more freely but wear faster, while honed edges provide greater durability at the cost of slightly increased cutting forces. For optimal performance in high-speed machining applications, consider end mills with specially engineered chip breakers that control chip formation and reduce heat buildup at the cutting zone.
Which End Mill Material Is Best for Your Specific Application?
The material composition of your end mill fundamentally determines its performance envelope, including maximum cutting speeds, temperature resistance, and wear characteristics. The three primary materials—High-Speed Steel (HSS), carbide, and ceramic—each offer distinct advantages and limitations that make them suitable for different machining scenarios.
Carbide end mills operate at speeds of 200-300 m/min and can machine materials up to 65 HRC, making them ideal for high-volume production. HSS tools, while limited to 60-100 m/min and materials up to 45 HRC, provide an economical solution for low-volume or budget-constrained operations. For extreme applications involving high-temperature alloys, ceramic end mills excel with incredible speeds of 500-800 m/min and hardness capabilities up to 75 HRC. Additionally, specialized coatings like TiAlN can triple wear resistance when machining stainless steel. These material considerations become particularly important when dealing with parts destined for industrial machinery, where durability and precision are paramount.

The performance gap between these materials becomes even more pronounced in challenging applications. Carbide tools maintain their cutting edge at temperatures up to 800°C, while HSS begins to lose hardness above 600°C. This temperature resistance directly translates to higher permissible cutting speeds and longer tool life. Furthermore, the rigidity of carbide (nearly three times that of HSS) reduces tool deflection, allowing for more aggressive cutting parameters and tighter tolerances. When selecting between these options, consider not just the initial tool cost but the total cost per part, including tool life, machine time, and surface quality requirements.
What Strategies Can You Implement to Achieve Perfect Surface Finish in End Milling?
Achieving exceptional surface finish requires a strategic approach that goes beyond basic machine settings. By implementing proven optimization techniques, you can dramatically improve your end milling results while simultaneously extending tool life and reducing production costs. These strategies focus on controlling cutting forces, managing heat generation, and minimizing vibration throughout the machining process.
Several key parameters directly influence surface quality. Controlling stepover within 30-50% of tool diameter creates the optimal balance between machining speed and surface finish. Implementing chip thinning calculations for radial depths below 50% prevents tool deflection and ensures consistent material removal. Additionally, advanced toolpath strategies like trochoidal milling can reduce heat buildup by 25% during pocket machining operations, dramatically improving surface consistency and dimensional accuracy. For applications where aesthetics and functionality both matter, understanding the nuances of surface finish standards and measurement methods becomes essential to achieving consistent, high-quality results.

Beyond these fundamental approaches, consider implementing variable depth of cut techniques to distribute wear evenly across the cutting edges, extending tool life while maintaining consistent surface quality. Controlling entry and exit conditions during milling operations also proves critical—a programmed arc-in approach reduces impact forces by gradually engaging the cutting edges with the workpiece material. For finishing operations, light spring passes (0.1-0.2mm) with increased spindle speed and reduced feed rate can achieve surface finishes as fine as Ra 0.4μm without specialized polishing operations. These techniques, when properly implemented, transform standard end milling operations into precision finishing processes.
Conclusion
Mastering end milling requires understanding the intricate relationship between cutting tool design, material properties, and machining parameters. By selecting the appropriate flute count and helix angle for your specific application, choosing the optimal tool material, and implementing proven optimization strategies, you can achieve superior results in terms of both productivity and surface quality. Whether you're machining aluminum components, hardened steel molds, or exotic aerospace alloys, the principles outlined in this guide provide a foundation for success in your end milling operations.
Remember that continuous improvement in end milling comes through systematic experimentation and data collection. Track your results, document successful parameters, and gradually refine your approach based on measurable outcomes. As machining technology continues to advance with innovations like variable flute designs and specialized coatings, staying informed about these developments will help you maintain a competitive edge in precision manufacturing.
[External Links Recommendation]
[American Society of Mechanical Engineers (ASME)][^1]
[CNC Machining Resource Center][^2]
[International Journal of Machine Tools and Manufacture][^3]
[End Milling][^4]
---
[^1]: Discover ASME's standards for machining processes to ensure compliance and improve the quality of your engineering projects.
[^2]: Explore the CNC Machining Resource Center for in-depth technical guides and resources that can enhance your understanding of end milling applications.
[^3]: Delve into the International Journal of Machine Tools and Manufacture for cutting-edge academic research that can inform your machining practices.
[^4]: Explore this link to understand the process, benefits, and applications of End Milling in manufacturing.
-
Posted in
End Milling