What Are The Most Precise CNC Turning Operations Used In Manufacturing?
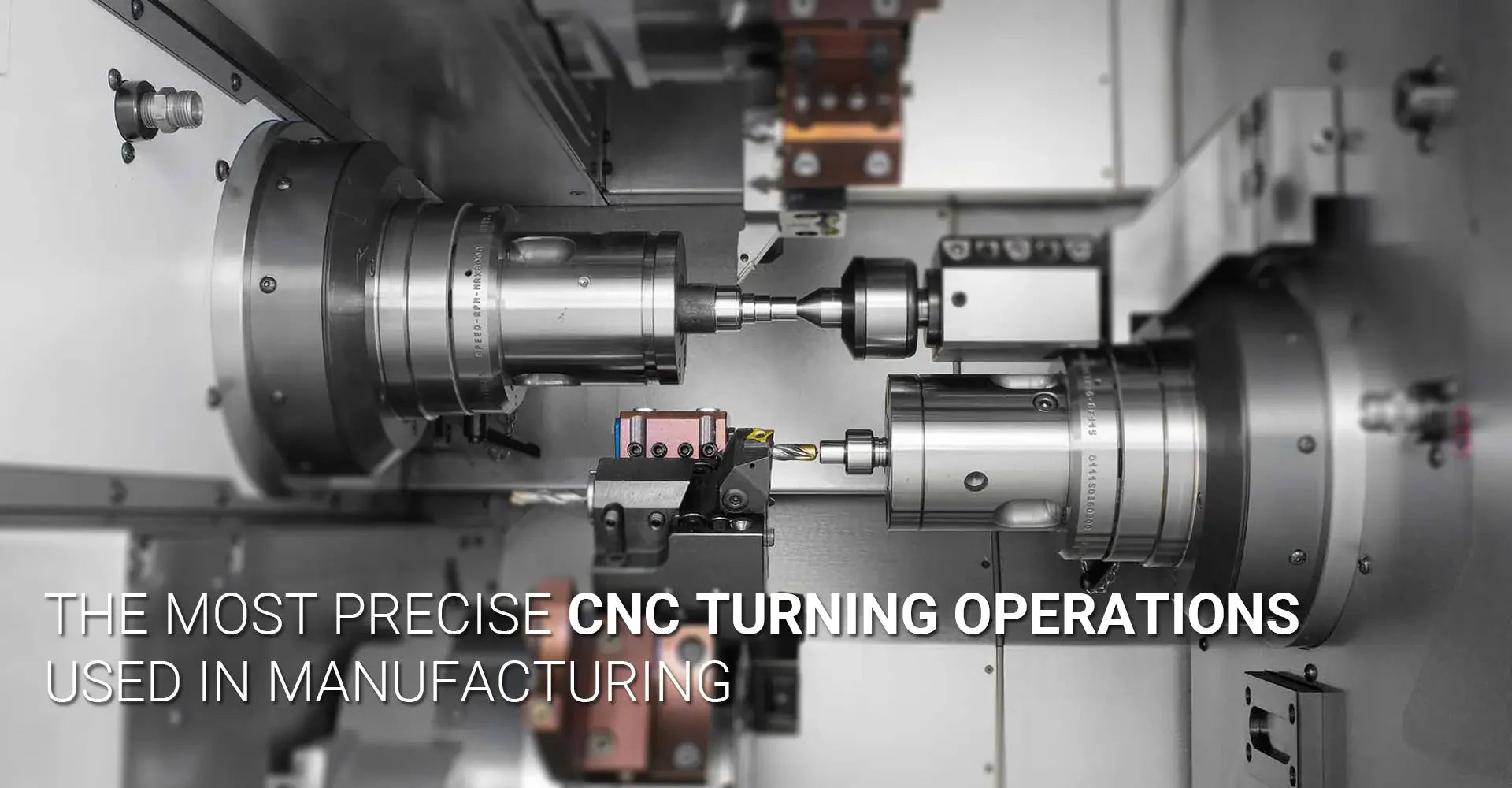
What Are The Most Precise CNC Turning Operations Used In Manufacturing?

Manufacturing precision has reached unprecedented levels through CNC turning operations, reshaping how industries create complex components. From aerospace components to automotive parts, CNC turning stands as a cornerstone of modern manufacturing precision.
Quick Overview: CNC turning operations transform raw materials into precise cylindrical parts through computer-controlled cutting processes. These techniques enable manufacturers to achieve tolerances as tight as ±0.0001 inches while maintaining consistent quality across production runs.
The realm of CNC turning encompasses various specialized operations, each serving unique manufacturing needs. Let's explore how these different techniques contribute to creating precise components for diverse industrial applications.
Table of Contents
- Basic CNC Turning Methods for Production Success
- Threading and Tapping Operations in Manufacturing
- Specialized CNC Turning Techniques for High-Precision
- Live Tooling Impact on CNC Operations
What Basic CNC Turning Methods Drive Production Success?
The foundation of precision manufacturing relies on fundamental CNC machining operations that shape raw materials into exact specifications.
Basic turning operations include facing, straight turning, and boring - each playing a crucial role in creating perfect cylindrical components. These methods form the backbone of manufacturing processes across industries.
These fundamental operations serve as building blocks for more complex manufacturing processes. Facing operations create perfectly flat surfaces perpendicular to the workpiece axis, while straight turning reduces the workpiece diameter to precise specifications. Boring operations expand and finish internal diameters with exceptional accuracy, particularly important in automotive components manufacturing.
How Do Threading and Tapping Operations Shape Manufacturing Results?
Threading and tapping operations represent specialized techniques that create both external and internal threads essential for component assembly.
These operations require precise control of cutting parameters to ensure proper thread engagement and surface finish quality.

Threading operations create external threads through carefully controlled helical cutting movements, while tapping focuses on internal thread creation. Both processes demand exact synchronization between spindle rotation and tool feed rates to achieve proper thread pitch and depth. Industries rely on these operations for creating everything from precision fasteners to complex mechanical assemblies.
Which Specialized CNC Turning Techniques Define High-Precision Production?
Advanced turning techniques elevate manufacturing capabilities through specialized tooling and multi-axis control systems.
Working with various materials from metals to plastics, these techniques enable manufacturers to achieve complex geometries and tight tolerances.

High-precision turning techniques include hard turning of hardened materials and Y-axis turning for off-center features. These capabilities allow manufacturers to produce complex components in a single setup, reducing production time while maintaining exceptional accuracy. The aerospace industry particularly benefits from these advanced techniques, contributing to the sector's 15% share of the global CNC machining market.
Hard turning represents a significant advancement in machining technology, allowing direct machining of hardened materials (up to 65 HRC) without requiring post-heat treatment grinding operations. This technique delivers several advantages:
- Surface finish quality matching or exceeding traditional grinding
- Reduced production time by eliminating secondary operations
- Lower energy consumption compared to grinding processes
- Greater flexibility in part geometry and features
Y-axis turning capabilities have introduced new possibilities for complex part production:
- Off-center feature machining without repositioning
- Enhanced milling capabilities during turning operations
- Improved tool positioning for better surface finish
- Reduced cycle times for complex geometries
The integration of sophisticated process monitoring systems further enhances these specialized techniques:
- Real-time tool wear monitoring
- Adaptive feed rate optimization
- In-process quality control measurements
- Automated error compensation systems
What Makes Live Tooling a Game-Changer in CNC Operations?
Live tooling transforms traditional turning centers into multi-tasking manufacturing powerhouses.
This technology enables milling, drilling, and other operations without moving the workpiece to different machines, dramatically increasing production efficiency.
Live tooling capabilities have revolutionized production processes by combining turning and milling operations in a single setup. This integration reduces handling time, improves accuracy, and contributes to the projected growth of the global CNC machining market, expected to reach USD 105.6 billion by 2027.
The impact of live tooling extends across multiple aspects of manufacturing:
Tool Configuration Options:
- Axial drilling and tapping tools
- Radial milling attachments
- Multi-tool turret configurations
- Adjustable angle heads for complex features
Operational Benefits:
- Single-setup completion of complex parts
- Reduced work-in-progress inventory
- Minimal part handling and transfer time
- Improved geometric accuracy through reduced setups
Application Versatility:
- Cross-hole drilling during turning operations
- Contour milling of irregular shapes
- Helical interpolation for large holes
- Thread milling in multiple orientations
Quality Improvements:
- Better concentricity between turned and milled features
- Reduced stack-up errors
- Improved process repeatability
- Enhanced surface finish consistency
The integration of live tooling with advanced CNC controls also enables:
- Synchronized spindle operations
- Multi-channel programming capabilities
- Simultaneous multi-axis movements
- Advanced tool path optimization
Conclusion
CNC turning operations continue to advance manufacturing capabilities through diverse techniques and technologies. From basic turning operations to advanced live tooling applications, these processes ensure precise component production across industries.
Key Takeaways:
- Basic turning operations provide the foundation for precision manufacturing
- Threading and tapping capabilities enable complex assembly requirements
- Specialized techniques expand manufacturing possibilities
- Live tooling integration enhances production efficiency
Recommended Resources
[CNC turning operations](https://www.xometry.com/resources/machining/types-of-turning-operations/)[^1]
[Y-axis turning](https://www.youtube.com/watch?v=SmhlTJez3fY)[^2]
[Live tooling](https://www.southernfabsales.com/blog/what-is-live-tooling)[^3]
---
[^1]: Understanding the various CNC turning operations can enhance your machining skills and efficiency. Explore this resource for detailed insights.
[^2]: Y-axis turning is crucial for complex part geometries. Discover its benefits and applications to improve your CNC knowledge.
[^3]: Live tooling allows for more versatile machining operations. Learn how it can optimize your production processes.
-
Posted in
CNC turning