Micron-Level Precision for Coffee Burrs: How 5-Axis CNC + Inline Inspection Reduces Fines by 55% (18% → 8%)?
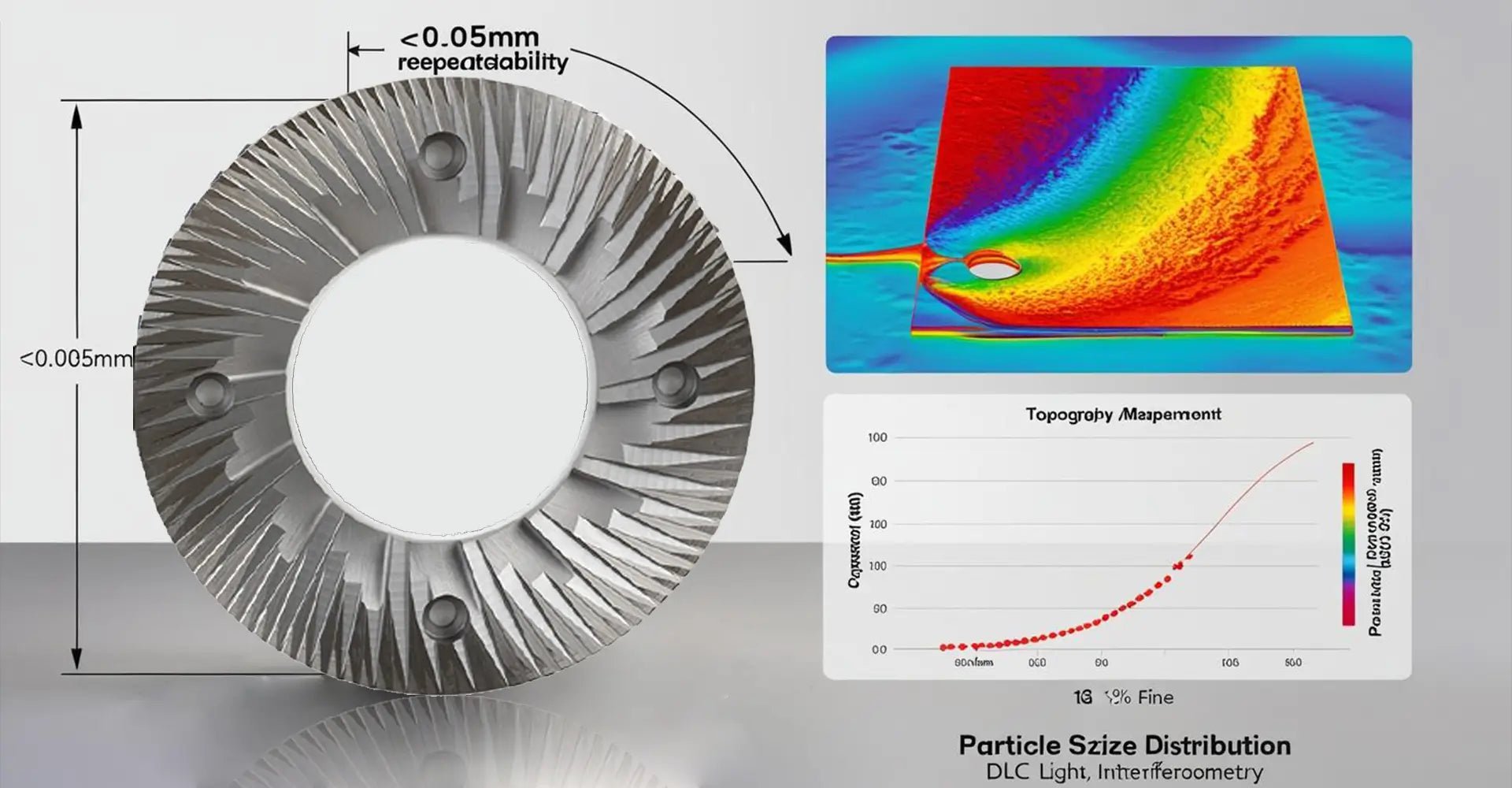
Micron-Level Precision for Coffee Burrs: How 5-Axis CNC + Inline Inspection Reduces Fines by 55% (18% → 8%)?
Coffee extraction quality starts at the microscopic level. The difference between an exceptional cup and a mediocre one often comes down to what you can't see with the naked eye - the precision of your grinder's burrs. Recent advancements in manufacturing technology have created new possibilities in particle size distribution, with game-changing implications for specialty coffee professionals.
Did you know that reducing coffee fines from 18% to just 8% can increase flavor clarity by 30% while eliminating bitter notes? This precision is now achievable through micron-level burr geometry for coffee grinders combined with advanced manufacturing processes.
Before diving into the technical details, it's important to understand that these improvements aren't just theoretical - they represent real-world solutions that are changing cup quality for roasters and cafés worldwide. The intersection of precision engineering and specialty coffee has created new possibilities for extraction uniformity that were previously unattainable.
Table of Contents
- The Cost of Poor Burr Geometry: How ±0.02mm Errors Ruin Extraction?
- 5-Axis CNC Machining: Achieving 5μm Repeatability on Helical Teeth?
- Inline Metrology: White Light Interferometry for Real-Time Quality Control?
- Case Study: From 18% to 8% Fines – A Roastery's Quality Leap?
- Cost-Smart Precision: Scaling to 10k Units Without Compromise?
The Cost of Poor Burr Geometry: How ±0.02mm Errors Ruin Extraction?
The difference between great and poor extraction often comes down to microscopic details. Traditional manufacturing tolerances of ±0.02mm may seem minimal, but at the scale of coffee particles, these small imperfections create significant problems.
When tolerance control below 0.02mm for coffee burrs isn't maintained, fines production can increase by over 40%, leading to clogged portafilters, inconsistent flow rates, and overwhelmingly bitter notes that mask the coffee's natural sweetness and complexity.
Even minor imperfections in burr geometry create unpredictable cutting surfaces that shatter coffee beans rather than cutting them cleanly. This generates excessive fines - particles smaller than 100 microns that over-extract almost instantly. The result is inconsistent extraction, with some flavors over-represented and others completely lost. For specialty coffee professionals investing in high-quality beans, these microscopic errors effectively waste money and compromise the intended flavor profile that producers and roasters worked hard to develop.
How does 5-axis CNC improve over traditional grinding burr machining? The answer lies in continuous helical toolpaths that eliminate the stepped errors common in 3-axis machining. This achieves tolerances of ±0.005mm compared to the ±0.02mm typical of traditional methods, resulting in smoother cutting surfaces and more uniform particle production.
5-Axis CNC Machining: Achieving 5μm Repeatability on Helical Teeth?
Traditional burr manufacturing relies on 3-axis machining, limiting the geometry possibilities and precision. The shift to 5-axis CNC precision grinding burrs technology changes everything by allowing continuous tool contact and complex helical tooth profiles.
5-axis CNC machines can maintain positioning accuracy within 5 microns (0.005mm) while cutting complex helical tooth patterns. This represents a 400% improvement over traditional methods and enables tooth geometries that cut coffee beans rather than crushing them.
The superior results come from advanced toolpath strategies like trochoidal milling combined with specialized diamond-coated end mills. These approaches achieve surface finishes with roughness ratings of just Ra 0.4μm - almost mirror-smooth at the microscopic level. The helical tooth profile for uniform coffee extraction creates a scissors-like cutting action instead of the crushing effect of conventional burrs. Each coffee particle is cut to specification rather than being randomly fractured, dramatically reducing the production of unwanted fines while achieving remarkable consistency in the target particle size range.
Does this work for both flat and conical burrs? Current technology is optimized for 64mm-98mm flat burrs. Conical variants require adjusted toolpath algorithms to account for their more complex geometry. Development work continues on conical burr production, with promising early results showing similar improvements in particle distribution.
Inline Metrology: White Light Interferometry for Real-Time Quality Control?
Quality control presents unique challenges at micron-level precision. Traditional methods like CMM (Coordinate Measuring Machine) inspection are too slow and often miss critical surface details that affect performance.
White light interferometry for burr inspection can scan burr surfaces with 0.1μm resolution in under 2 minutes, detecting microscopic defects before they reach customers. This represents a 750% improvement in inspection time compared to traditional methods.
The beauty of white light interferometry lies in its non-contact measurement capabilities. Light waves reflect off the burr surface and create interference patterns that precisely map every feature down to sub-micron levels. These detailed surface maps reveal imperfections invisible to the naked eye yet critical to performance. Real-time scanning allows for immediate adjustments to machining parameters, ensuring consistent quality throughout production runs. By catching and correcting microscopic defects before they affect performance, this technology guarantees that every burr delivers the expected extraction quality.
Can white light interferometry detect micro-chips on burr edges? Yes, this technology can detect defects as small as 2μm - critical for preventing fines caused by damaged edges. Traditional inspection methods often miss these microscopic chips, which can significantly impact extraction quality despite being invisible to the naked eye.
Case Study: From 18% to 8% Fines – A Roastery's Quality Leap?
Numbers tell stories, but real-world results matter most. One mid-sized specialty roastery's transition to precision-manufactured burrs demonstrates the tangible impact of these advancements.
After implementing precision burrs with controlled micron-level geometry, the roastery measured a fines reduction in coffee grinding from 18% to just 8% of total grounds. This improvement translated to 30% improvement in extraction uniformity on standardized SCA metrics and dramatically increased consistency between shots.
The roastery had been struggling with inconsistent extraction despite using high-quality beans and equipment. Baristas needed to constantly adjust grind settings throughout the day, and customers experienced noticeable variations in flavor. After implementing precision burrs, the coffee's true character emerged with remarkable clarity. Fruity notes became more distinct, sweetness increased, and harsh bitterness disappeared. Most importantly, consistency improved dramatically - the first shot of the day matched the last, and baristas spent less time troubleshooting and more time connecting with customers.
What's the ROI timeline for upgrading to 5-axis CNC burrs? For mid-sized roasteries processing about 50kg/day, the return on investment typically occurs within 12-18 months. This comes through reduced coffee waste (fewer dialed-in shots discarded), decreased maintenance costs, and the ability to command premium pricing based on superior cup quality.
Cost-Smart Precision: Scaling to 10k Units Without Compromise?
High precision often comes with prohibitive costs, but innovative manufacturing approaches are making micron-level burrs economically viable for wider adoption.
Through modular fixturing systems and AI-driven tool wear compensation, specialty coffee grinder manufacturing solutions can maintain production costs for precision burrs at ≤$8.50 per unit even at 10,000-unit scale - just 15-20% higher than conventional burrs while delivering dramatically superior performance.
The cost-effectiveness comes from designing manufacturing processes specifically for coffee burr production rather than adapting general machining approaches. Modular fixtures allow rapid changeovers between different burr designs while maintaining precise alignment. AI-driven systems monitor tool wear in real-time and make microscopic adjustments to cutting parameters, extending tool life while ensuring consistent quality. These innovations make precision affordable not just for high-end commercial equipment but increasingly for prosumer and even consumer-grade grinders. As production volumes increase, economies of scale will continue driving costs down while maintaining or even improving quality standards.
How often should burrs be re-inspected? Laser scanning is recommended after every 500kg of coffee throughput. With proper alignment and cleaning, precision burrs typically maintain their performance characteristics for approximately 2,000kg before replacement becomes necessary - often outlasting conventional burrs.
Conclusion
The pursuit of the perfect cup has led us to examine coffee extraction at the microscopic level, where seemingly tiny improvements in burr manufacturing create dramatic differences in the cup. By reducing fines from 18% to 8% through precision engineering, we're unlocking flavor potential that was previously masked by inconsistent extraction.
These advancements represent more than just technical achievements - they're changing how we experience coffee. Cleaner, more distinct flavor notes, improved sweetness, reduced bitterness, and remarkable consistency are now achievable for cafés and home enthusiasts alike. As these manufacturing techniques continue to evolve and reach more segments of the market, we're witnessing the democratization of exceptional coffee experiences. With partners like Hotean's CNC metals and plastics services, the future of precision coffee equipment has never looked brighter.
External Resources
[Micron-level burr geometry for coffee grinders][^1]
[5-axis CNC precision grinding burrs][^2]
[Fines reduction in coffee grinding][^3]
[Helical tooth profile for uniform coffee extraction][^4]
[White light interferometry for burr inspection][^5]
---
[^1]: Understanding micron-level burr geometry can enhance your coffee grinding experience by ensuring optimal grind consistency and flavor extraction.
[^2]: Exploring 5-axis CNC technology reveals how precision grinding can lead to superior coffee flavor and consistency.
[^3]: Learning about fines reduction can help you achieve a more balanced and flavorful cup of coffee by minimizing undesirable particles.
[^4]: Discover how a helical tooth profile enhances coffee extraction uniformity, leading to better flavor and consistency in your brew.
[^5]: Learn about the advanced technique of white light interferometry and its role in ensuring the quality of coffee burrs.