Anti-Deformation Machining for Ultra-Thin Coffee Machine Housings: How Can You Achieve ±0.03mm Flatness?
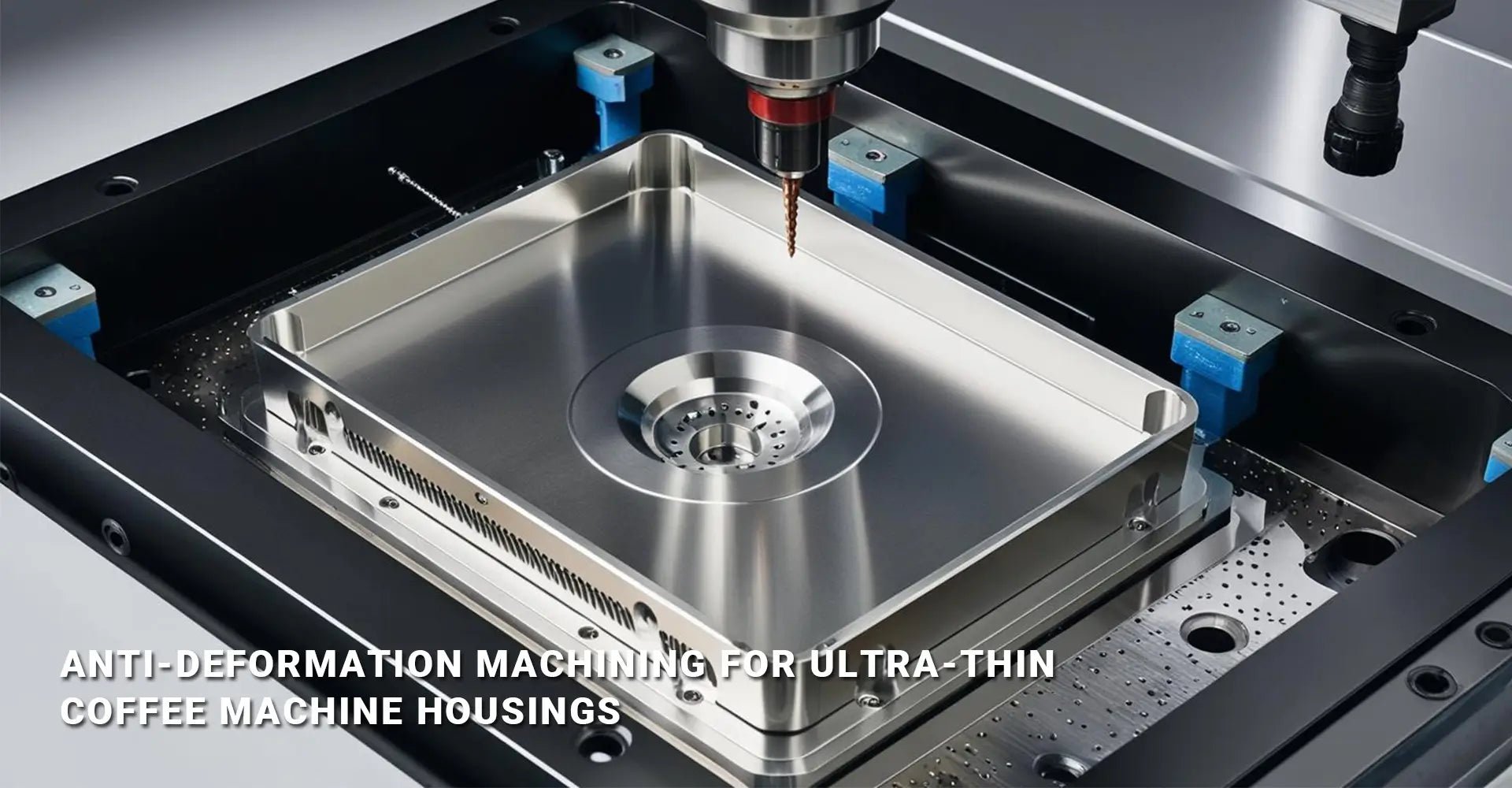
Anti-Deformation Machining for Ultra-Thin Coffee Machine Housings: How Can You Achieve ±0.03mm Flatness?
Conquering the Machining Challenge of Portable Coffee Device Shells
Have you been struggling with warping in ultra-thin aluminum coffee machine housings? You're not alone. Manufacturers across the premium portable coffee device sector face significant challenges when machining shells with 1.2mm thickness. The precision requirements for these sleek, lightweight devices demand flatness tolerances of ±0.03mm – a standard that conventional machining approaches frequently fail to meet.
Key Insight: Achieving ±0.03mm flatness in ultra-thin aluminum coffee machine housings requires specialized vacuum fixturing combined with cryogenic cooling techniques – reducing scrap rates by up to 90%.
The combination of vacuum fixturing and controlled low-temperature cooling represents a breakthrough for portable espresso machine manufacturers struggling with shell deformation. This approach eliminates the primary causes of warping while maintaining production efficiency.
Table of Contents
- Why Do 1.2mm Aluminum Shells Deform Beyond 0.1mm?
- How Does Vacuum Fixturing Eliminate Deformation in Delicate Geometries?
- What Role Does Cryogenic Cooling Play in Stress-Free Machining?
- How Did One Swiss Brand Achieve 0.03mm Flatness Consistency?
- What Cost Benefits Come with Advanced Anti-Deformation Techniques?
Why Do 1.2mm Aluminum Shells Deform Beyond 0.1mm?
The machining of ultra-thin aluminum housings frequently results in warping that exceeds acceptable tolerances, especially when traditional clamping and cooling methods are employed. The primary culprits behind this deformation include thermal stress, excessive clamping pressure, and residual material strain.
Critical Data: Standard machining approaches typically result in flatness deviations of 0.1-0.15mm in 1.2mm aluminum shells – far exceeding the ±0.03mm tolerance required for premium portable coffee devices.
When aluminum sheets with 1.2mm thickness undergo machining, they become particularly susceptible to deformation due to their minimal material mass. The heat generated during cutting operations causes uneven thermal expansion, while conventional clamping systems apply concentrated pressure points that imprint onto the final product. Additionally, the inherent material properties of aluminum alloys mean they retain internal stresses that manifest as warping after machining operations are complete.
Anti-deformation machining for ultra-thin coffee machine housings represents a specialized approach that addresses these challenges by minimizing stress introduction during the manufacturing process.
How Does Vacuum Fixturing Eliminate Deformation in Delicate Geometries?
Vacuum fixturing represents a paradigm shift in securing ultra-thin workpieces during machining operations, distributing holding forces evenly across the entire surface rather than at discrete points.
Technical Specification: Modular vacuum systems operating at 0.6kPa with silicone seals adapt to curved surfaces with radii ≥10mm, maintaining workpiece stability without introducing deformation.
The vacuum fixturing approach uses specialized suction pads arranged in configurable patterns to accommodate various housing designs. Unlike mechanical clamps that concentrate force at specific points, vacuum systems distribute pressure uniformly across the workpiece surface. This elimination of localized pressure prevents the introduction of stress points that would otherwise lead to warping.
For portable coffee machine housings with complex curved surfaces, silicon seals create airtight connections even on surfaces with radii as tight as 10mm. This flexibility allows manufacturers to secure intricate geometries without compromising the anti-deformation benefits of vacuum fixturing.
Vacuum fixturing for 1.2mm aluminum parts has become the gold standard for achieving consistent results in ultra-thin components where traditional clamping would introduce unacceptable deformation.
What Role Does Cryogenic Cooling Play in Stress-Free Machining?
Low-temperature coolant systems represent a critical component in achieving flatness control for ultra-thin aluminum parts, addressing the thermal-induced stresses that conventional cooling methods fail to manage.
Performance Metric: CO₂/liquid nitrogen hybrid cooling systems reduce toolpath-induced heat by 70%, maintaining consistent material temperatures throughout the machining process.
Cryogenic cooling systems utilize specialized coolant maintained at approximately -20°C, dramatically reducing thermal expansion during machining operations. By maintaining consistent material temperatures throughout the cutting process, these systems prevent the development of thermal gradients that would otherwise cause uneven expansion and subsequent warping.
The implementation of CO₂/liquid nitrogen hybrid cooling technologies offers precise temperature control without risking aluminum embrittlement. This approach maintains workpiece temperature within the optimal processing range, preventing both thermal stress and potential material property changes. Post-machining annealing processes further ensure the restoration of material ductility while preserving dimensional stability.
Low-temperature coolant in thin-wall machining has proven essential for achieving consistent flatness control in premium portable coffee device components.
How Did One Swiss Brand Achieve 0.03mm Flatness Consistency?
A leading Swiss portable espresso machine manufacturer faced significant challenges with their premium ultra-thin aluminum housings, experiencing scrap rates approaching 40% due to warping issues.
Case Study Result: By implementing the vacuum fixturing and cryogenic cooling workflow, scrap rates decreased from 40% to under 4%, while achieving consistent ±0.03mm flatness across production batches.
The manufacturer's journey began with a comprehensive analysis of their existing production workflow, identifying thermal stress during machining and clamping pressure as the primary deformation sources. After implementing a custom vacuum fixturing system designed specifically for their housing geometry, they observed immediate improvements in flatness control.
The integration of cryogenic cooling further enhanced results, allowing them to maintain thermal stability throughout the machining process. The combined approach resulted in housings that consistently achieved the required ±0.03mm flatness tolerance. Quality verification using laser scanning technology confirmed compliance with ISO 10360-2 standards, generating 3D deviation maps with ±0.005mm repeatability to document the improvements.
This case study represents a breakthrough in portable espresso machine shell warping solutions, demonstrating how targeted process improvements can resolve previously intractable manufacturing challenges.
What Cost Benefits Come with Advanced Anti-Deformation Techniques?
While implementing vacuum fixturing and cryogenic cooling technologies requires initial investment, the financial benefits quickly outweigh these costs through reduced waste and rework requirements.
ROI Analysis: A $3,800 investment in tooling and process modifications saves manufacturers approximately $12,000 monthly in reduced scrap and rework costs – delivering a 30% overall cost reduction compared to traditional methods.
The financial benefits extend beyond mere scrap reduction. Implementing these advanced anti-deformation techniques allows manufacturers to maintain tighter tolerances consistently, enhancing product quality and reducing assembly challenges. The improved flatness control enables better component fit, reducing assembly time and increasing final product quality.
CNC machining services that incorporate these specialized approaches can deliver significant advantages for companies producing premium portable coffee equipment. Cost-effective strategies for portable device manufacturing often center on reducing waste and rework, making these techniques particularly valuable despite their initial implementation costs.
Conclusion
Achieving exceptional flatness control ±0.03mm for appliance housings requires specialized approaches that address the unique challenges of these delicate components. The combination of vacuum fixturing and cryogenic cooling represents a proven methodology for maintaining precision tolerances in production environments.
By eliminating the concentrated pressure points of traditional clamping systems and controlling thermal stress through specialized cooling, manufacturers can dramatically improve quality while reducing costs. The case studies and technical specifications outlined demonstrate how aluminum alloy thin-wall CNC precision control techniques deliver consistent results across various housing designs.
Warp prevention in lightweight aluminum shells ultimately depends on a comprehensive approach that addresses both mechanical and thermal factors simultaneously. When properly implemented, these techniques transform what was once a manufacturing limitation into a competitive advantage for premium portable coffee device manufacturers.
External Resources
[Portable espresso machine shell warping solutions][^1]
[Aluminum alloy thin-wall CNC precision control][^2]
[Vacuum fixturing for 1.2mm aluminum parts][^3]
[Low-temperature coolant in thin-wall machining][^4]
[Flatness control ±0.03mm for appliance housings][^5]
---
[^1]: Discover effective solutions to prevent warping, ensuring your portable espresso machine maintains its shape and functionality over time.
[^2]: Learn about CNC precision control techniques that optimize machining processes for aluminum alloys, enhancing product quality and efficiency.
[^3]: Explore this link to understand how vacuum fixturing enhances precision in machining aluminum parts, especially at thin dimensions.
[^4]: Discover the benefits of using low-temperature coolant in thin-wall machining to improve surface finish and reduce thermal distortion.
[^5]: Learn about techniques to achieve precise flatness control in appliance housings, crucial for quality and performance.