What Are The 6 Critical Aspects of High Pressure Die Casting?
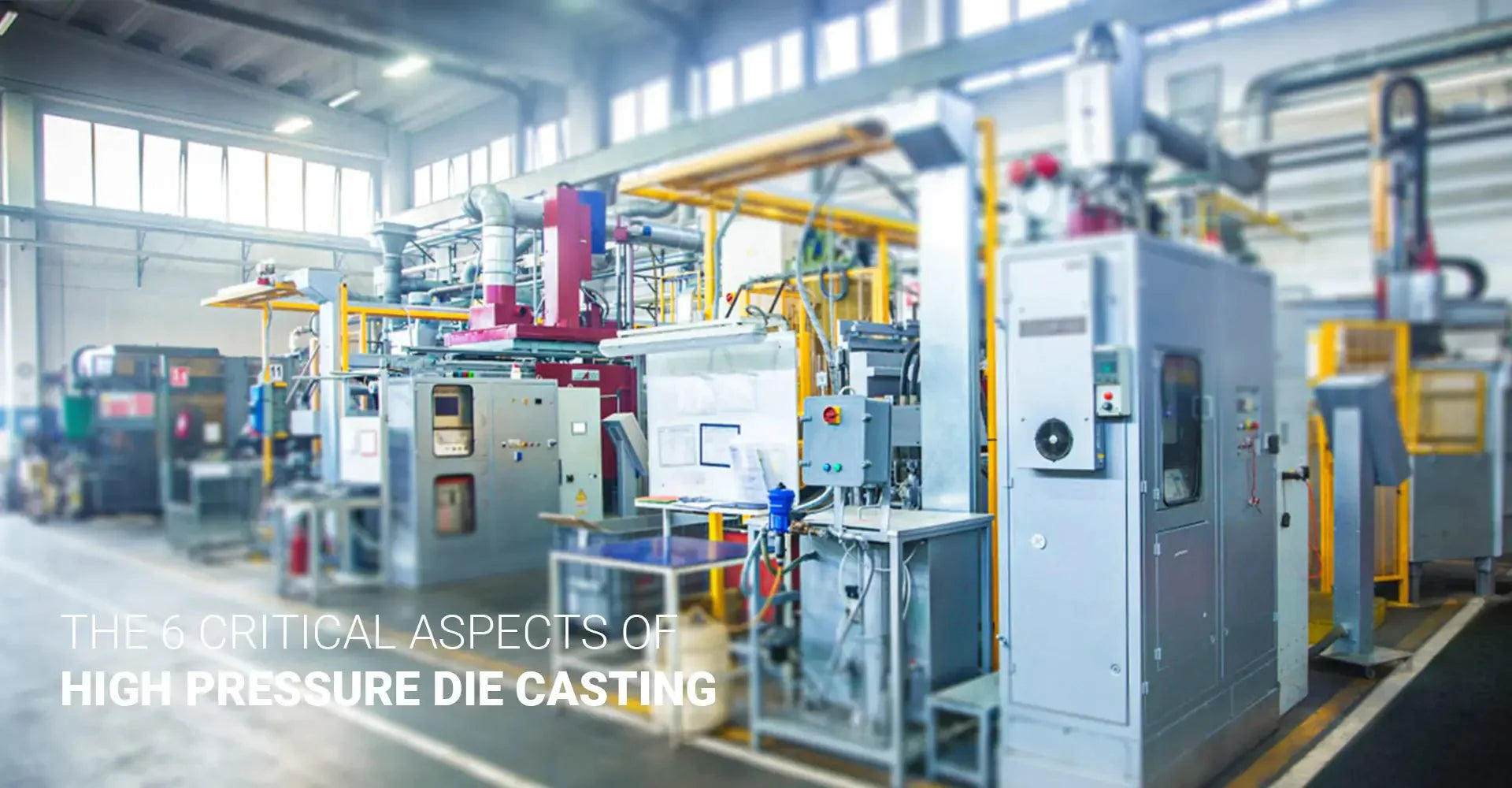
What Are The 6 Critical Aspects of High Pressure Die Casting?

High pressure die casting (HPDC) stands as one of manufacturing's most versatile and efficient processes. This advanced metal forming technique delivers precision parts at high volumes, making it indispensable across multiple industries. As we explore the critical aspects of HPDC, you'll discover why this technology continues to shape modern manufacturing.
The global HPDC market's explosive growth - from $36.42 billion in 2023 to an expected $49.11 billion by 2028 - reflects its increasing adoption across industries. Whether you're an industry professional seeking deeper insights or a business owner exploring manufacturing options, understanding these six critical aspects will help you make informed decisions about high pressure die casting solutions.
Let's dive into the essential elements that make HPDC a cornerstone of modern manufacturing, from process fundamentals to future innovations.
Table of Contents
- Is High Pressure Die Casting Revolutionizing Modern Manufacturing?
- What Materials Drive Success in High Pressure Die Casting?
- How Does Quality Control Transform HPDC Production?
- Why is HPDC Leading in Cost-Effective Manufacturing?
- Can High Pressure Die Casting Meet Sustainability Goals?
- What's Next for High Pressure Die Casting Technology?
Is High Pressure Die Casting Revolutionizing Modern Manufacturing?
The foundation of HPDC's success lies in its remarkable ability to produce complex components with exceptional precision. This revolutionary process involves injecting molten metal into a mold at pressures ranging from 1,500 to 25,000 PSI, creating parts with outstanding surface finish and dimensional accuracy.
Manufacturing sectors worldwide increasingly rely on HPDC for its unmatched capabilities. The automotive industry particularly benefits from this technology, producing everything from engine blocks to transmission cases with unprecedented efficiency. With cycle times as short as 10-100 milliseconds, HPDC enables high-volume production while maintaining exceptional quality standards.
Modern manufacturing facilities leverage HPDC's versatility to create components for various applications, from kitchen appliances to electronic devices. The process's ability to produce thin-walled sections with excellent detail makes it invaluable across diverse manufacturing sectors.
What Materials Drive Success in High Pressure Die Casting?
The selection of appropriate materials plays a crucial role in successful HPDC operations. Different metals and alloys offer varying benefits, each suited to specific applications and requirements.
Aluminum alloys dominate the HPDC landscape, prized for their excellent strength-to-weight ratio and corrosion resistance. These properties make them ideal for automotive components and consumer electronics housings. Zinc alloys, meanwhile, excel in producing intricate details and thin walls, perfect for decorative and functional parts in consumer products.
Material | Properties | Applications |
---|---|---|
Aluminum Alloys | - Lightweight | - Automotive parts |
- Corrosion-resistant | - Consumer electronics | |
- High strength | ||
Zinc Alloys | - Excellent castability | - Electronics |
- Low melting point | - Hardware components | |
- Cost-effective | ||
Magnesium Alloys | - Very lightweight | - Aerospace components |
- High strength-to-weight ratio | - Automotive parts | |
- Good machinability |
Material selection criteria extend beyond basic mechanical properties to include factors like thermal conductivity, fluidity, and cost-effectiveness. The right choice depends on the specific application requirements and desired performance characteristics of the final product.
How Does Quality Control Transform HPDC Production?
Quality control in HPDC represents a comprehensive approach to ensuring consistent, high-quality outputs. Modern manufacturing facilities employ sophisticated monitoring systems and testing protocols throughout the production process.
Real-time monitoring of crucial parameters like temperature, pressure, and injection speed helps maintain optimal production conditions. Advanced techniques such as X-ray inspection and ultrasonic testing enable thorough examination of internal structures, ensuring parts meet stringent quality standards.

The implementation of robust quality control measures has transformed HPDC from a traditional manufacturing process to a precision-driven technology. This evolution has enabled manufacturers to achieve remarkable consistency while minimizing defects and waste.
Why is HPDC Leading in Cost-Effective Manufacturing?
The economics of HPDC present a compelling case for its adoption in modern manufacturing. With material utilization rates reaching 90-98%, the process minimizes waste and maximizes resource efficiency.
Initial tooling costs, while significant, are offset by the ability to produce large volumes of complex parts quickly and consistently. The high automation potential further reduces labor costs while improving productivity and quality consistency.
The long-term cost benefits of HPDC become particularly apparent in high-volume production scenarios, where the initial investment is amortized across large production runs.
Can High Pressure Die Casting Meet Sustainability Goals?
Environmental considerations increasingly influence manufacturing decisions, and HPDC rises to meet these challenges. The industry's focus on sustainability manifests in several key areas.
Modern HPDC operations emphasize energy efficiency through improved furnace design and process optimization. The high material utilization rate significantly reduces waste, while advanced recycling programs ensure that scrap metal is effectively reused in the production cycle.

The implementation of closed-loop systems and energy recovery technologies further enhances the environmental profile of HPDC operations.
What's Next for High Pressure Die Casting Technology?
The future of HPDC promises exciting developments in both technology and applications. Industry innovations focus on increasing efficiency, improving quality, and expanding the range of possible applications.
Emerging technologies like artificial intelligence and machine learning are being integrated into HPDC processes, enabling predictive maintenance and real-time quality control. These advances promise to further enhance production efficiency and part quality.
![next-generation HPDC technology and applications]](https://cdn.shopify.com/s/files/1/0915/0434/5380/files/Future-focused_visualization_showing_next-generation_HPDC_technology_and_applications.webp?v=1736229681)
The integration of digital twins and Industry 4.0 principles continues to push the boundaries of what's possible in HPDC manufacturing.
Conclusion
High pressure die casting stands at the forefront of modern manufacturing technology, offering unmatched capabilities in producing complex, high-quality components efficiently. Its continued evolution, driven by technological advances and sustainability concerns, ensures its place as a crucial manufacturing process for years to come.
The industry's growth trajectory, supported by innovations in materials, processes, and quality control, points to an exciting future for HPDC technology. As manufacturing continues to evolve, HPDC will undoubtedly play a pivotal role in shaping the future of production across diverse industries.
External Links and Resources
-
Posted in
die casting, high pressure die casting