CNC Machining vs Injection Molding: Which Manufacturing Process Best Fits Your Project in 2025?
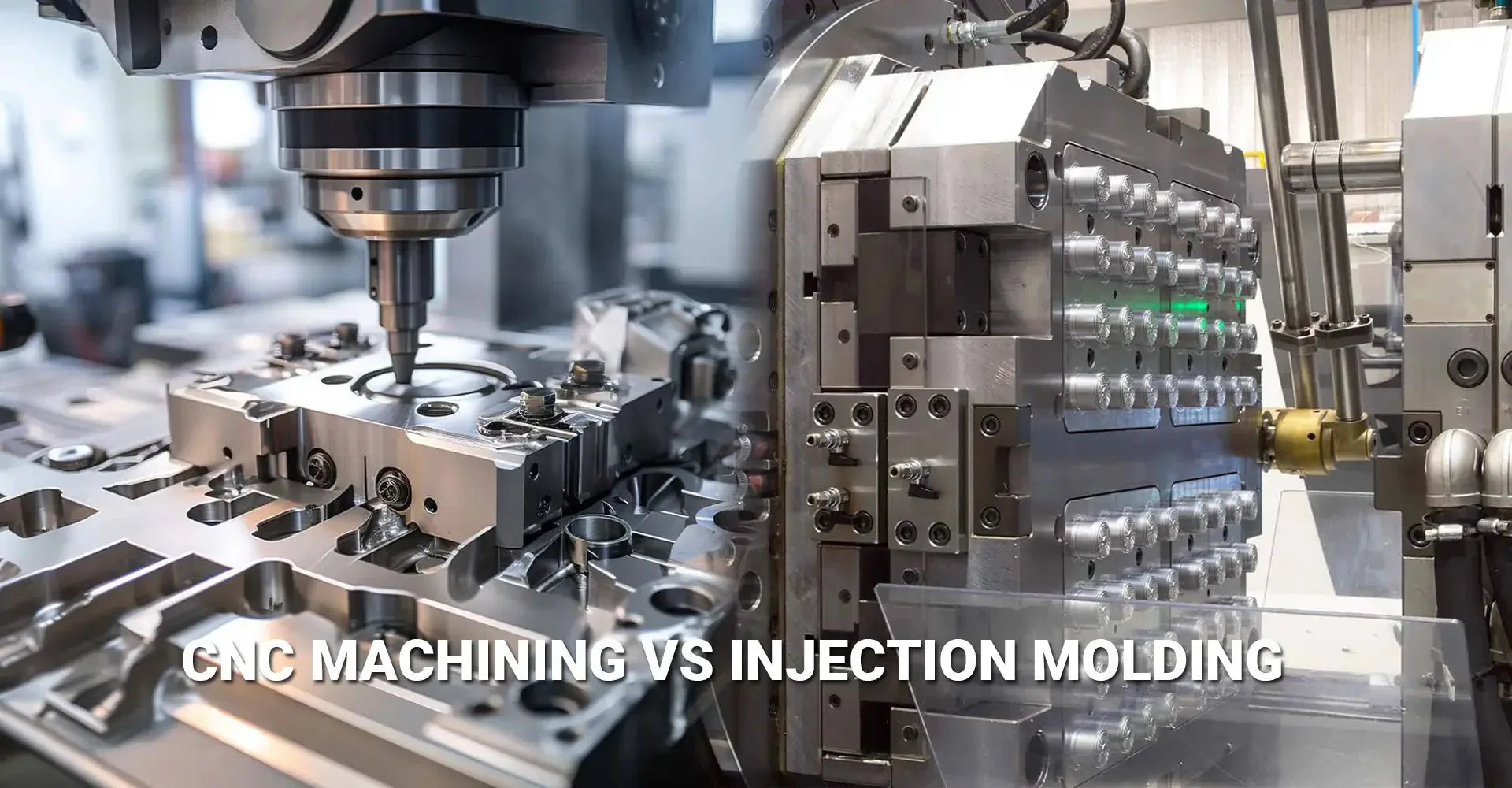
CNC Machining vs Injection Molding: Which Manufacturing Process Best Fits Your Project in 2025?

When it comes to modern manufacturing, choosing between CNC machining and injection molding can significantly impact your project's success. Both methods offer unique advantages and limitations that can affect cost, quality, and production efficiency. Whether you're a product developer, engineer, or manufacturing professional, understanding these differences is crucial for making informed decisions.
CNC machining is a subtractive manufacturing process that precisely removes material from a solid block to create parts, while injection molding involves injecting molten material into a mold cavity. Each method serves different manufacturing needs, from prototyping to mass production, with varying cost implications and production capabilities.
To help you make the best choice for your manufacturing needs, let's dive deep into a comprehensive comparison of these two manufacturing processes, examining everything from costs and materials to design considerations and quality outcomes.
[Table of Contents]
- What Are CNC Machining and Injection Molding Manufacturing Methods?
- How Do Production Costs Compare Between CNC Machining and Injection Molding?
- Which Method Offers Better Production Efficiency and Volume Capabilities?
- What Materials Can You Use in Each Manufacturing Process?
- How Do Design Limitations Affect Your Manufacturing Choice?
- Which Process Delivers Better Quality and Precision Results?
- Conclusion: Making the Right Choice for Your Manufacturing Needs
What Are CNC Machining and Injection Molding Manufacturing Methods?
CNC machining and injection molding represent two fundamentally different approaches to manufacturing. CNC machining uses computer-controlled cutting tools to remove material from a solid block, creating precise parts through programmed instructions. In contrast, injection molding involves heating plastic materials until molten, then injecting them into a pre-made mold under high pressure.
The key distinction lies in their fundamental approaches: CNC machining is subtractive, removing unwanted material to create the final part, while injection molding is additive, filling a cavity with material to form the desired shape. This basic difference influences everything from cost structure to production capabilities.
Understanding these manufacturing processes requires considering their operational principles. CNC machining offers immediate production capability with minimal setup, making it ideal for prototypes and small batches. Injection molding, while requiring significant initial setup with mold creation, excels in high-volume production scenarios where thousands of identical parts are needed.
How Do Production Costs Compare Between CNC Machining and Injection Molding?
Cost considerations between these methods vary dramatically based on production volume. Initial setup costs for CNC machining are relatively low, typically involving only programming and material costs. Injection molding requires substantial upfront investment in mold creation, ranging from $10,000 to over $100,000 depending on complexity.
The break-even point between these methods typically occurs around 5,000 to 10,000 units. Below this threshold, CNC machining often proves more economical. Above it, injection molding's lower per-unit costs make it increasingly cost-effective as volumes rise.
When calculating total production costs, consider factors beyond just per-unit pricing. CNC machining costs remain relatively consistent per part but include material waste and longer processing times. Injection molding's costs are front-loaded but decrease significantly with volume, often reaching mere cents per part in large production runs.
Which Method Offers Better Production Efficiency and Volume Capabilities?
Production efficiency varies significantly between these methods. Surface finish quality and production speed are key factors in determining overall efficiency. Injection molding can produce hundreds or thousands of parts per hour once operational, while CNC machining typically produces fewer parts but offers more flexibility in design changes.
Injection molding excels in high-volume scenarios, capable of producing a part every few seconds in automated systems. CNC machining, while slower, offers consistent quality and the ability to make immediate design modifications without additional tooling costs.
The efficiency equation isn't just about speed. CNC machining offers quick startup and modification capabilities, making it ideal for prototyping and small-batch production. Injection molding's efficiency shines in mass production, where its high output and minimal operator intervention significantly reduce per-unit costs.
What Materials Can You Use in Each Manufacturing Process?
Material selection significantly impacts the choice between CNC machining and injection molding. CNC machining accommodates a broader range of materials, including metals, plastics, wood, and composites. Injection molding primarily works with thermoplastics and thermosetting polymers, though some metal injection molding (MIM) applications exist.
While CNC machining can work with virtually any solid material that can be cut, injection molding requires materials that can be melted and solidified repeatedly. Common injection molding materials include ABS, polycarbonate, and nylon, while CNC machining frequently uses aluminum, steel, titanium, and engineering plastics.
Material properties play a crucial role in process selection. CNC machining excels with harder materials requiring precise tolerances, while injection molding works best with materials having good flow properties and consistent shrinkage rates. The choice of material affects not only the manufacturing process but also the final product's performance characteristics.
How Do Design Limitations Affect Your Manufacturing Choice?
Design considerations often determine which manufacturing method is most suitable. CNC machining excels at creating complex external geometries and precise features but faces limitations with internal cavities due to tool access restrictions. Injection molding can produce complex internal and external features simultaneously but requires careful consideration of draft angles and wall thickness.
Each method has distinct design constraints. Injection molding requires consistent wall thickness and draft angles for part removal, while CNC machining needs to account for tool reach and cutting path accessibility. Understanding these limitations is crucial for optimizing design for manufacturing (DFM).

The impact of design complexity varies between processes. While CNC machining might require multiple setups for complex geometries, injection molding can produce intricate parts in a single shot. However, injection molding requires more upfront design consideration to prevent issues like sink marks, warp, and incomplete fills.
Which Process Delivers Better Quality and Precision Results?
Quality and precision capabilities differ significantly between CNC machining and injection molding. CNC machining typically achieves tighter tolerances and better surface finishes directly from the machine, while injection molding's quality depends heavily on mold design and process control.
CNC machining can routinely achieve tolerances of ±0.0005 inches, while injection molding typically manages ±0.005 inches. Surface finish quality in CNC machining is highly controllable through cutting parameters and tool selection, offering various textures and finishes to meet specific requirements.
Both processes can deliver high-quality parts when properly executed. CNC machining offers consistent quality across small batches with minimal variation between parts. Injection molding, while potentially showing more variation, can maintain good quality control in high-volume production through careful process monitoring and control.
Conclusion: Making the Right Choice for Your Manufacturing Needs
The selection between CNC machining and injection molding ultimately depends on several key factors:
- Production volume requirements
- Material selection needs
- Design Complexity
- Quality and tolerance requirements
- Budget constraints
- Time-to-market considerations
Consider these factors carefully when choosing between processes, as each offers distinct advantages for different manufacturing scenarios.
External Links and Resources:
-
Posted in
CNC machining, Injection molding