Die Casting vs 3D Printing: Which is Better for Your Appliance Manufacturing Needs?
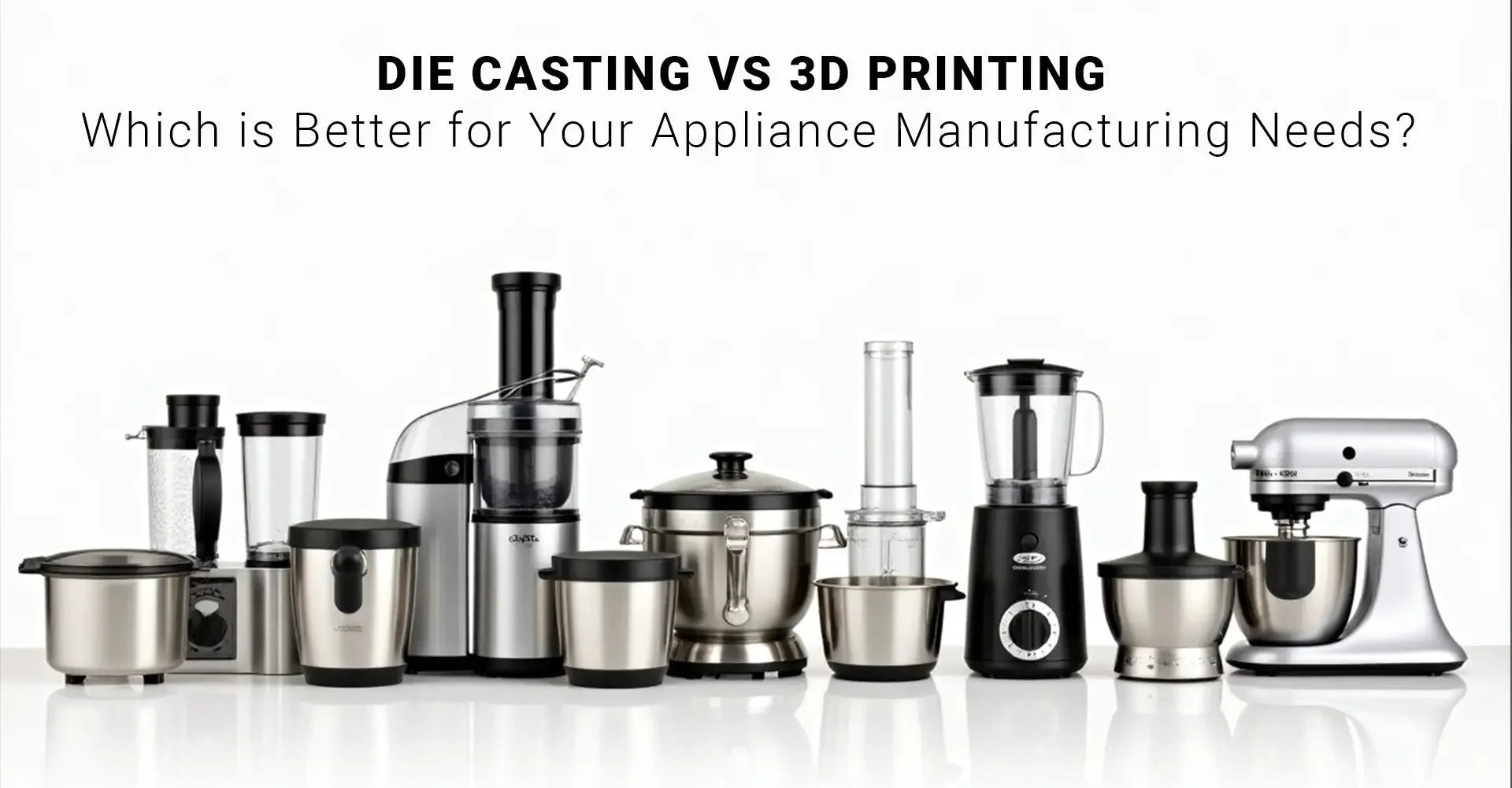
Die Casting vs 3D Printing: Which is Better for Your Appliance Manufacturing Needs?

When manufacturing kitchen appliance housings, choosing between die casting and 3D printing can significantly impact your production costs, timelines, and product quality. Each method offers distinct advantages depending on your production volume, material requirements, and design complexity. This comprehensive guide examines both manufacturing processes to help you make an informed decision for your specific appliance manufacturing needs.
Die casting excels in high-volume production with superior durability and heat resistance, while 3D printing offers unmatched design flexibility and cost-effective prototyping. For kitchen appliance housings, die casting typically becomes more economical around 1,000 units, whereas 3D printing dominates for customized designs and small batch production. Your choice ultimately depends on production scale, material requirements, and design complexity.
Before diving into the specifics of each manufacturing method, let's examine the key factors that differentiate die casting from 3D printing in appliance manufacturing. Understanding these fundamental differences will help you determine which process aligns best with your project requirements and achieve cost-effective kitchen appliance housing production.
[Table of Contents]
- What Are the Key Differences Between Die Casting and 3D Printing for Appliance Manufacturing?
- When Should You Choose Die Casting for Appliance Manufacturing?
- What Makes 3D Printing Advantageous for Certain Appliance Applications?
- How Do Material Considerations Impact Your Manufacturing Choice?
- What Are the Cost Implications Between Die Casting and 3D Printing?
- Conclusion
What Are the Key Differences Between Die Casting and 3D Printing for Appliance Manufacturing?
Die casting and 3D printing represent two fundamentally different approaches to creating appliance components. Die casting involves injecting molten metal into reusable molds under high pressure, creating durable, precise parts with excellent thermal properties. In contrast, 3D printing builds objects layer by layer from various materials, allowing for complex geometries without tooling costs. These core differences drive their suitability for different appliance manufacturing scenarios.
Die casting offers production speeds up to 20-60 parts per hour for medium-sized appliance housings, while 3D printing might produce only 1-2 parts in the same timeframe. However, 3D printing eliminates the 2-6 week mold creation process, enabling faster initial production. Die casting typically uses aluminum and zinc alloys with excellent heat resistance, while 3D printing employs various plastics and resins with more limited thermal properties.
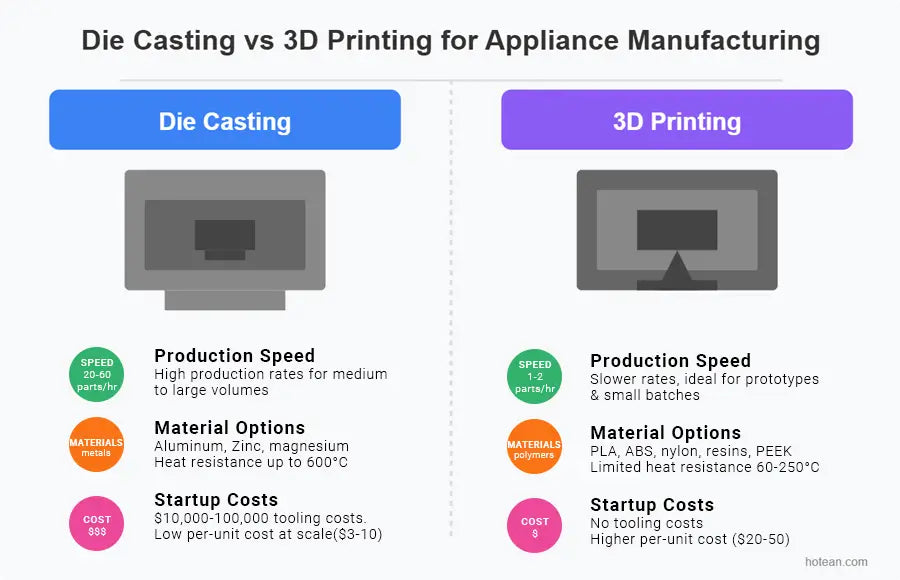
Material selection for die casting vs 3D printing represents another critical distinction between these methods. Die casting primarily uses metals like aluminum, zinc, and magnesium alloys, providing excellent thermal conductivity and structural integrity for appliances that generate heat. Meanwhile, 3D printing offers a wider range of materials, from standard thermoplastics like ABS and PLA to engineering-grade polymers like nylon and PEEK. Additionally, die casting requires significant upfront investment but scales efficiently, whereas 3D printing has minimal startup costs but higher per-unit expenses that remain relatively constant regardless of volume. This fundamental difference highlights the contrast between high-volume vs low-volume appliance manufacturing strategies.
When Should You Choose Die Casting for Appliance Manufacturing?
Die casting shines when manufacturing large quantities of identical parts with consistent quality and durability requirements. For appliance manufacturers aiming to produce thousands of units with reliable performance, die casting offers unmatched efficiency and cost-effectiveness. The process creates parts with excellent dimensional stability, smooth surface finish, and the thermal resistance necessary for many kitchen appliances.
Die casting becomes economically advantageous beyond approximately 1,000 units, where the cost per part drops to $3-$10 for medium-sized appliance housings. The process achieves tolerances of ±0.25mm, creating consistent parts with wall thicknesses as thin as 0.5mm. For appliances requiring heat resistance, die-cast aluminum alloys maintain structural integrity at temperatures up to 600°C, making them ideal for ovens, toasters, and other heat-generating kitchen appliances.

Beyond raw production numbers, die casting offers several practical advantages for appliance manufacturing. The process creates parts with excellent electromagnetic interference (EMI) shielding properties, crucial for modern smart appliances. Die-cast components also provide superior impact resistance and durability, extending product lifespans. Furthermore, the smooth surface finish achieved through die casting (with roughness values as low as Ra ≤1.6μm) minimizes the need for post-processing, reducing labor costs and production time for consumer-facing appliance components where aesthetics matter significantly. These benefits make die casting particularly valuable for mass production in appliance design, where consistency and durability are paramount concerns.
What Makes 3D Printing Advantageous for Certain Appliance Applications?
3D printing excels in scenarios where design flexibility, rapid prototyping, and customization are paramount. For appliance manufacturers developing new products or producing specialized, low-volume items, 3D printing eliminates tooling costs and enables iterative design improvements. The technology allows for complex internal geometries and integrated features that would be impossible or prohibitively expensive with traditional manufacturing methods.
3D printing enables design iterations in days rather than weeks, with prototype costs typically 40-60% lower than die casting alternatives. For small production runs under 100 units, 3D printing can reduce total costs by 30-50% compared to die casting. The process accommodates complex geometries like internal cooling channels, honeycomb structures for weight reduction, and integrated snap-fit features that would require multiple die-cast parts and assembly operations.

Beyond prototyping vs mass production in appliance design, 3D printing enables mass customization for specialty appliance markets. Manufacturers can economically produce customized or regional variants without investing in additional tooling. Advanced 3D printing technologies like SLA (Stereolithography) achieve surface finishes approaching injection molding quality (Ra ≤3.2μm), suitable for visible appliance components with appropriate post-processing. Additionally, 3D printing allows for just-in-time production, reducing inventory costs and enabling more responsive supply chains—particularly valuable for legacy or specialty appliance parts that would otherwise require expensive minimum order quantities through traditional manufacturing. This flexibility highlights the advantage of 3D printing for low-volume appliance manufacturing scenarios.
How Do Material Considerations Impact Your Manufacturing Choice?
Material selection for die casting vs 3D printing represents a critical factor when choosing between these methods for appliance manufacturing. Die casting primarily utilizes metal alloys with excellent thermal properties and durability, while 3D printing offers a broader range of polymers and composites with varying performance characteristics. Understanding these material differences helps ensure your manufacturing choice aligns with your appliance's functional requirements.
Die-cast aluminum alloys maintain structural integrity at temperatures up to 600°C with thermal conductivity around 96-167 W/m·K, making them ideal for heat-generating appliances. In contrast, most standard 3D printing materials like PLA and ABS begin to deform at 60-105°C, though specialized materials like PEEK maintain properties up to 250°C. Die-cast zinc alloys offer excellent corrosion resistance and fine detail capabilities, while 3D printing materials like nylon provide superior impact resistance and flexibility for components requiring shock absorption.
Beyond temperature resistance, consider how each manufacturing method affects material performance. Die casting creates parts with consistent material properties throughout, while 3D printed objects often exhibit anisotropic behavior—stronger in some directions than others due to layer orientation. This characteristic particularly affects load-bearing appliance components. Additionally, die-cast metals provide natural EMI shielding properties essential for electronic appliances, whereas 3D printed parts typically require conductive additives or coatings to achieve similar functionality. For food-contact applications in kitchen appliances, die-cast aluminum offers established food safety compliance, while 3D printing materials require careful selection from FDA-approved options like certain grades of nylon or polypropylene. Thermal resistance in kitchen appliance materials remains a crucial consideration when selecting between these manufacturing methods.
What Are the Cost Implications Between Die Casting and 3D Printing?
Understanding the cost structures of die casting versus 3D printing is essential for making financially sound manufacturing decisions. Die casting involves significant upfront investment but decreasing per-unit costs at scale, while 3D printing offers minimal initial investment but relatively consistent per-unit expenses regardless of volume. This fundamental difference creates distinct crossover points where each method becomes more economical for cost-effective kitchen appliance housing production.
Die casting molds typically cost $10,000-$100,000 depending on complexity but can produce hundreds of thousands of parts, driving per-unit costs down to $3-$10 for medium-sized appliance housings at high volumes. Conversely, 3D printing eliminates tooling costs but maintains relatively stable per-unit expenses of $20-$50 for similar parts regardless of quantity. The breakeven point typically occurs around 500-1,000 units, though this varies with part complexity, material selection, and quality requirements.
Beyond direct manufacturing costs, consider how each method impacts your total cost of ownership. Die casting's consistent, high-quality output reduces quality control and rejection rates compared to 3D printing's greater variability, particularly for large production runs. However, 3D printing minimizes inventory costs through on-demand production and eliminates expenses associated with design changes that would require new molds in die casting. Labor costs also differ significantly—die casting requires skilled operators for setup but runs efficiently afterward, while 3D printing needs minimal setup but more extensive post-processing labor for surface finish requirements for appliance housings. Additionally, sustainability in die casting and 3D printing presents different environmental and cost considerations, with die casting offering more recyclable materials but higher energy consumption, while 3D printing typically generates less waste during production but uses materials that may be more challenging to recycle.
Conclusion
When selecting between die casting and 3D printing for appliance manufacturing, consider your specific production volume, material requirements, design complexity, and timeline. Die casting offers superior economics for high-volume production with excellent durability and thermal performance, making it ideal for mainstream appliance housings. Conversely, 3D printing provides unmatched design flexibility, cost-effective prototyping, and economical small-batch production for customized or specialized appliance components.
Many successful manufacturers implement hybrid approaches, using 3D printing for prototyping and initial market testing before transitioning to die casting for full-scale production. Others leverage 3D printing for complex components while die casting simpler, high-volume parts. By understanding the strengths and limitations of each manufacturing method, you can optimize your production strategy to balance cost, quality, and time-to-market for your specific appliance manufacturing needs. The die casting vs 3D printing for appliance manufacturing decision ultimately depends on finding the right balance between production volume, material requirements, and surface finish quality for your specific appliance products.
[External Links Recommendation]
[Die Casting vs 3D Printing for Appliance Manufacturing][^1]
[Cost-Effective Kitchen Appliance Housing Production][^2]
[Thermal Resistance in Kitchen Appliance Materials][^3]
---
[^1]: This link will help you compare these two manufacturing methods, aiding in informed decision-making for production processes.
[^2]: Exploring this resource will provide insights into efficient manufacturing techniques that can save costs and improve quality in appliance production.
[^3]: Understanding thermal resistance is crucial for selecting materials that ensure safety and efficiency in kitchen appliances.
-
Posted in
3D Printing, die casting