Preventing Corrosion in Coffee Machine Metal Parts: The Complete Manufacturing Guide?
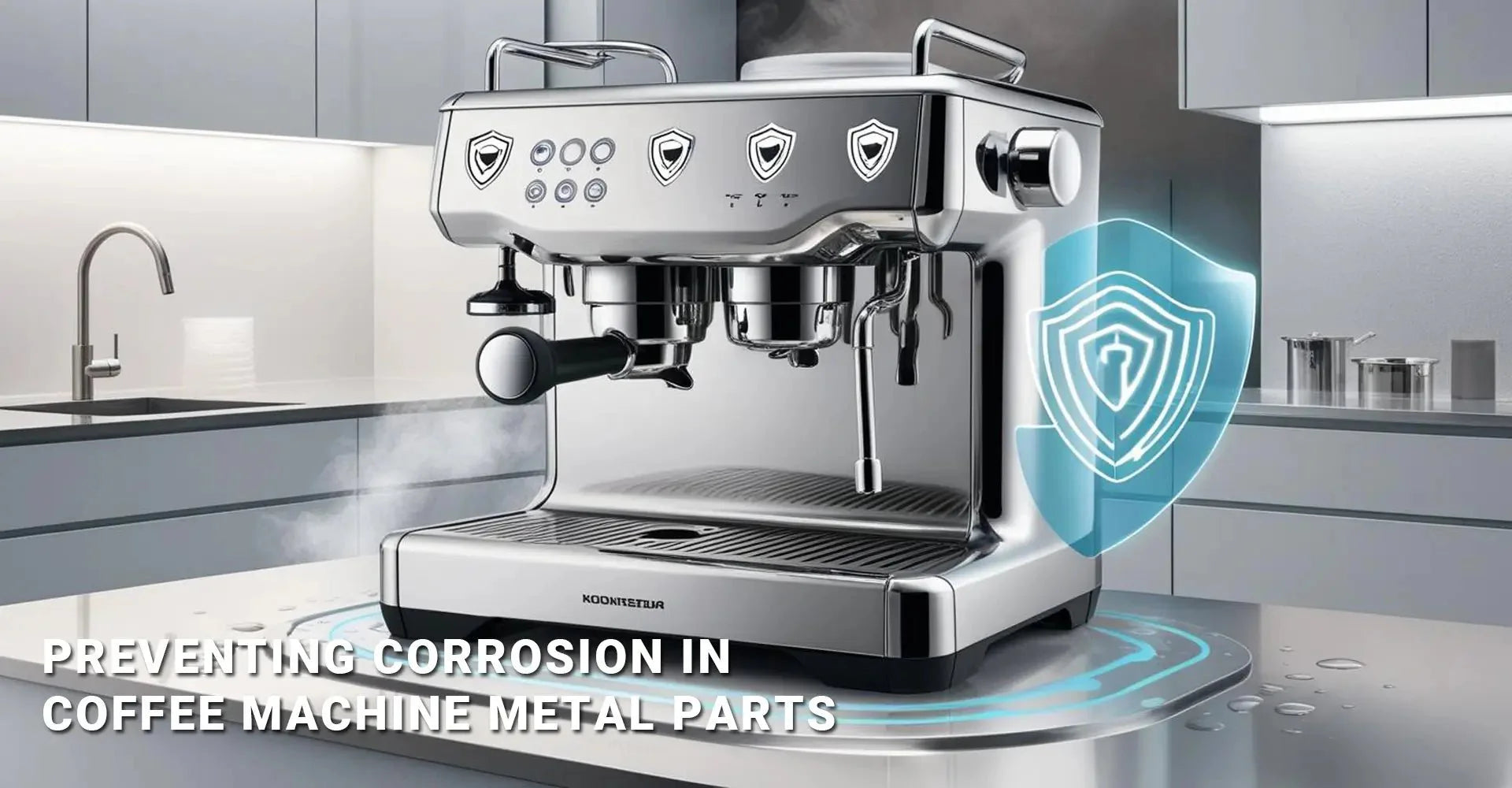
Preventing Corrosion in Coffee Machine Metal Parts: The Complete Manufacturing Guide?
Coffee machines operate in challenging environments where heat, moisture, and acidic compounds constantly threaten metal integrity. For manufacturers, preventing corrosion isn't just about aesthetics—it's crucial for food safety compliance, product longevity, and maintaining brand reputation. This comprehensive guide walks you through proven corrosion prevention for coffee machine metal parts strategies from initial design concepts to final mass production. Following a proper anti-corrosion approach is essential for creating durable metal components for coffee machines that withstand years of daily use.
Did you know? Studies show that over 67% of coffee machine warranty claims involve corroded components, while implementing proper anti-corrosion measures can extend product lifespan by 3-5 years and reduce maintenance costs by up to 40%. The right corrosion prevention strategy is vital for both consumer satisfaction and manufacturing profitability. This guide provides a practical anti-corrosion guide for appliances with a special focus on coffee equipment manufacturing challenges.
Let's explore the practical steps manufacturers can take throughout the entire production process to ensure coffee machine components remain corrosion-free, even in demanding household and commercial environments. This guide covers everything from design to mass production: anti-corrosion guide for appliances that will help you deliver durable, food-safe products to market. Whether you're manufacturing small batches or scaling up to mass production, these principles apply to all stages of coffee machine development.
[Table of Contents]
- What Makes Coffee Machine Components Vulnerable to Corrosion?
- Which Materials Provide the Best Corrosion Resistance for Coffee Applications?
- How Do Surface Treatments Enhance Corrosion Protection?
- What Testing Methods Validate Corrosion Resistance Before Mass Production?
- Conclusion
What Makes Coffee Machine Components Vulnerable to Corrosion?
Coffee machines create the perfect storm for corrosion with their unique combination of high temperatures, water exposure, and contact with acidic coffee compounds. Additionally, descaling agents containing citric or acetic acid further accelerate metal degradation if proper protective measures aren't in place. Understanding these specific challenges is the first step toward effective prevention. Manufacturers of coffee equipment must account for these factors when designing durable products.
Key Corrosion Factors: Heat cycles between 90-96°C, constant moisture exposure, acidic coffee oils (pH 5.0-5.5), mineral deposits from hard water, and aggressive cleaning solutions create multiple corrosion mechanisms that simultaneously attack metal surfaces. These factors make corrosion prevention for coffee machine metal parts particularly challenging compared to other kitchen appliances.
Different parts of coffee machines face varying corrosion risks. Boilers and heating elements must withstand high-temperature water exposure, while dispensing components manage acidic coffee oils and grounds. Exterior metal parts, meanwhile, must resist humidity and cleaning products. Each area requires a tailored approach to corrosion prevention based on these specific environmental stressors. Furthermore, galvanic corrosion becomes a significant concern when dissimilar metals come into contact in the presence of an electrolyte like water or coffee. Precision CNC machining services can help create components with tight tolerances that minimize water traps and potential corrosion sites.
Which Materials Provide the Best Corrosion Resistance for Coffee Applications?
Selecting the right base material is fundamental to corrosion prevention. For coffee machines, manufacturers typically choose between various grades of stainless steel for food-safe applications, aluminum alloys, and in some cases, coated carbon steel. Each option offers different benefits in terms of corrosion resistance, cost, machinability, and compliance with food safety regulations. The selection of appropriate CNC metals and plastics is a crucial first step in creating durable metal components for coffee machines.
Material Comparison: AISI 304 stainless steel offers excellent general corrosion resistance at moderate cost ($4-7/kg), while AISI 316 provides superior protection against acidic solutions but at a 15-30% price premium. Aluminum with proper anodizing delivers lightweight alternatives at $2-4/kg but requires more careful maintenance. These considerations are essential when developing cost-effective anti-corrosion solutions for small batches of specialty coffee equipment.
Laboratory tests demonstrate that AISI 316 stainless steel shows negligible weight loss (less than 0.001g/cm²/year) when exposed to typical coffee machine conditions, while untreated aluminum can deteriorate at rates up to 0.25g/cm²/year. Beyond material type, component geometry significantly impacts corrosion susceptibility—sharp corners, crevices, and horizontal surfaces that collect moisture accelerate degradation. Smart design practices include incorporating drainage channels, eliminating water traps, and ensuring proper ventilation to reduce condensation build-up on critical components. This comprehensive from design to mass production: anti-corrosion guide for appliances approach considers both material properties and structural design elements.
How Do Surface Treatments Enhance Corrosion Protection?
Even with ideal base materials, surface treatments often provide essential additional protection. Coffee machine manufacturers can choose from numerous surface finish options including electroplating, anodizing, passivation, powder coating, and emerging technologies like PVD (Physical Vapor Deposition). Each offers distinct advantages for different components and production volumes. Understanding the differences between electroplating vs powder coating for corrosion resistance helps manufacturers select the optimal solution for each component.
Treatment Effectiveness: Independent testing shows electroless nickel plating provides up to 1,000 hours of salt spray resistance (ASTM B117), while standard zinc plating typically achieves only 96-240 hours. Food-grade powder coatings can reach 500+ hours but require careful application to avoid holidays (coating gaps). These metrics are crucial when developing corrosion prevention for coffee machine metal parts strategies that meet or exceed industry standards.
The effectiveness of surface treatments depends heavily on proper application parameters. For instance, anodized aluminum requires precise control of current density, electrolyte composition, and treatment time—variations of just 10% can reduce corrosion protection by up to 40%. Similarly, stainless steel passivation demands exact acid concentration and immersion time to develop the optimal chromium oxide layer. When selecting treatments, manufacturers must also consider substrate compatibility, processing temperature limitations, and potential hydrogen embrittlement risks with certain high-strength components. These technical considerations are particularly important when developing durable metal components for coffee machines that must withstand years of use in challenging environments.
What Testing Methods Validate Corrosion Resistance Before Mass Production?
Thorough testing before scaling to mass production prevents costly quality issues and warranty claims. Industry-standard protocols like salt spray testing standards for kitchen appliances, humidity chamber exposure, and immersion tests provide quantifiable data on corrosion resistance. Additionally, accelerated life testing simulates years of use in weeks or months, helping identify potential weaknesses before products reach consumers. These validation procedures are an essential part of any from design to mass production: anti-corrosion guide for appliances.
Testing Standards: Coffee machine components typically require 240-500 hours of salt spray resistance (ASTM B117/ISO 9227), humidity chamber testing at 40°C/95% RH for 1,000 hours (ASTM D2247), and cyclic testing alternating between these conditions (ASTM G85) to simulate real-world performance. These rigorous tests help ensure that cost-effective anti-corrosion solutions for small batches will perform as well as mass-produced components.
While standardized tests provide valuable comparative data, manufacturers should also develop application-specific protocols. For instance, exposure to actual coffee extracts, descaling solutions, and cleaning agents more accurately predicts field performance than generic salt spray tests alone. Leading manufacturers supplement standard tests with custom procedures like thermal cycling (from room temperature to 100°C) while exposed to coffee solutions, or abrasion resistance after repeated cleaning cycles. These combined approaches identify potential failure modes that single-parameter tests might miss. Thorough testing ensures that durable metal components for coffee machines maintain their integrity throughout their intended service life.
Conclusion
Manufacturing durable, corrosion-resistant coffee machine components requires careful attention throughout the entire production process. From initial material selection and design considerations to appropriate surface treatments and rigorous testing protocols, each step contributes to the final product's performance and longevity. By implementing the strategies outlined in this guide, manufacturers can deliver high-quality coffee machines that maintain their functionality, appearance, and food safety compliance throughout their intended service life. Working with experienced partners who understand the unique challenges of corrosion prevention for coffee machine metal parts can significantly improve outcomes.
By following this comprehensive approach to corrosion prevention, manufacturers can achieve significant improvements in product quality while potentially reducing warranty claims by up to 60%. Remember that corrosion prevention is an investment that pays dividends through enhanced brand reputation, reduced service costs, and increased customer satisfaction. The most successful manufacturers approach corrosion prevention as an integral part of the design process rather than an afterthought. This from design to mass production: anti-corrosion guide for appliances provides the foundation for developing coffee machines with exceptional durability and performance. Partners like Hotean offer comprehensive CNC machining services and surface finish options that support these best practices.
[External Links Recommendation]
[electroplating vs powder coating][^1]
[Salt Spray Testing Standards for Kitchen Appliances][^2]
[Cost-Effective Anti-Corrosion Solutions for Small Batches][^3]
---
[^1]: Understanding the differences can help you choose the best finish for your projects, enhancing durability and aesthetics.
[^2]: Exploring these standards ensures your appliances meet quality and durability benchmarks, crucial for consumer safety.
[^3]: Discovering these solutions can save you money while ensuring the longevity of your products in small-scale production.
-
Posted in
surface finish