How Can Zinc Alloy Coffee Machine Handles Achieve 0.5% Porosity & 98% Plating Yield?
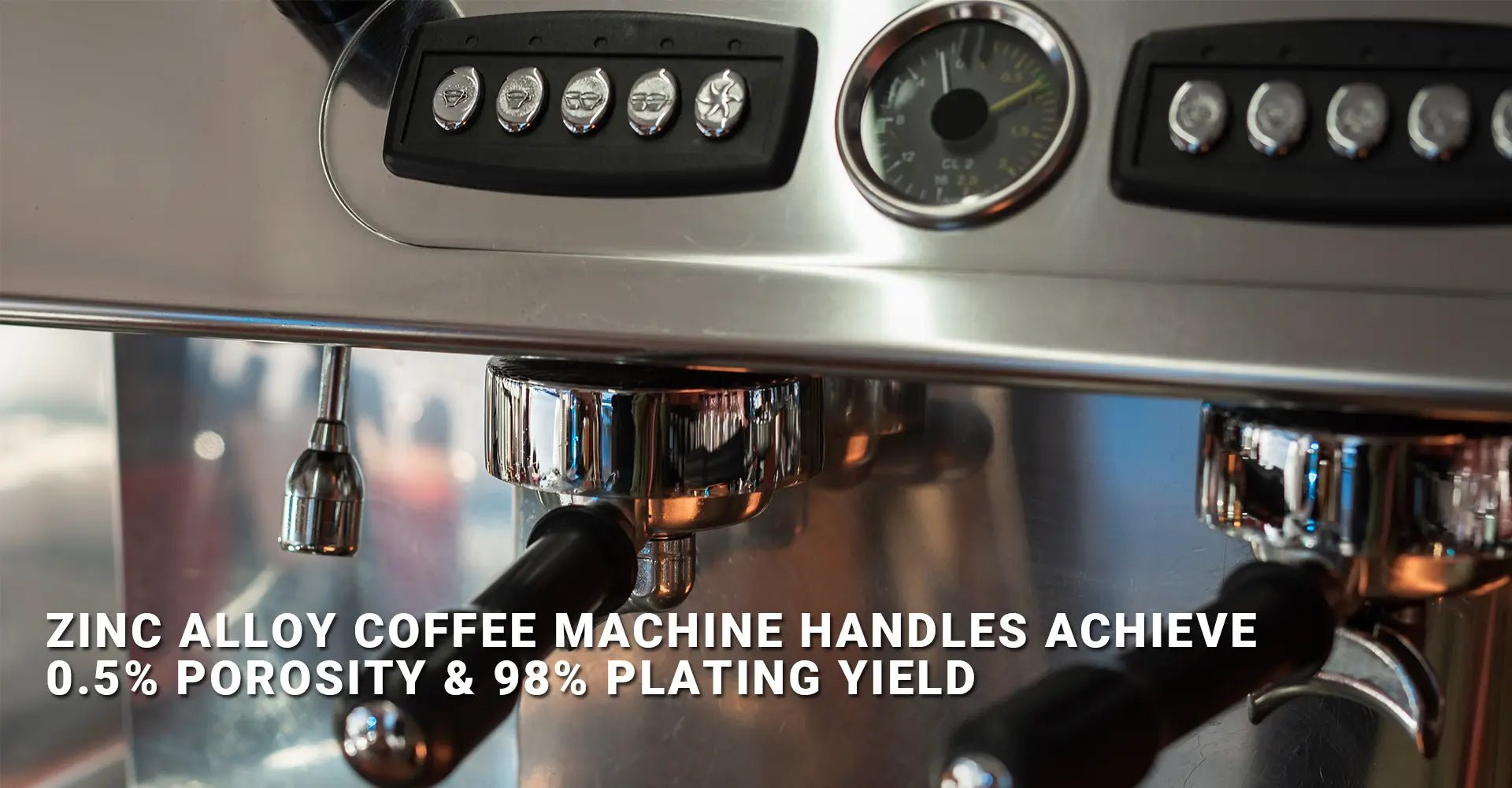
How Can Zinc Alloy Coffee Machine Handles Achieve 0.5% Porosity & 98% Plating Yield?
Struggling with plating failures on zinc alloy coffee machine handles? The hidden culprit is likely porosity—microscopic air pockets trapped during the casting process that wreak havoc on your finish quality and production yields. For manufacturers seeking to eliminate these costly defects, vacuum die casting for coffee machine handles now offers a proven solution that reduces porosity from 2% to an impressive 0.5%, dramatically boosting plating success rates to 98%.
- ✓ Vacuum die casting reduces porosity from 2% to 0.5% in zinc alloy coffee machine handles
- ✓ Advanced mold flow analysis eliminates trapped gases and ensures uniform metal fill
- ✓ Improved plating yield from 70% to 98%, saving manufacturers $28,000/month in reduced scrap
- ✓ ISO 9001-certified processes guarantee consistent quality across high-volume production runs
In this comprehensive guide, we'll explore how vacuum-assisted die casting techniques specifically address the challenges of producing high-quality coffee machine handles. You'll discover the science behind zinc alloy die casting porosity control, practical implementation strategies, and the substantial cost benefits that come from investing in these advanced casting methodologies.
[Table Of Contents]
- Why Do Air Voids Damage Your Coffee Machine Handle Plating?
- How Does Vacuum Die Casting Extract 99.8% of Air from Molten Zinc?
- What Role Does Mold Flow Analysis Play in Gate Design Success?
- How Do Real Production Numbers Prove the Value of Porosity Control?
- Conclusion
Why Do Air Voids Damage Your Coffee Machine Handle Plating?
The sleek chrome or nickel finishes that give coffee machine handles their premium look depend entirely on the quality of the substrate beneath. Unfortunately, conventional zinc alloy die casting often leaves microscopic air pockets—typically around 2% by volume—trapped within the metal structure. These nearly invisible defects become painfully apparent during electroplating processes.
- Trapped gas pockets expand during plating heat cycles, causing blistering
- Porosity creates weak adhesion points where plating chemicals can't properly bond
- Each 1% increase in porosity correlates to a 15% decrease in plating success rate
- ASTM E505 standards identify problematic void patterns typically concentrated at thick-to-thin transitions
Moreover, the location of porosity matters as much as the percentage. Research shows that handle grip areas—where design often requires thicker cross-sections—are particularly susceptible to gas entrapment. When traditional die casting machines inject molten zinc at velocities exceeding 50m/s, turbulence forces air into the metal flow. Additionally, the rapid solidification of zinc alloys (typically 6-8 seconds) doesn't allow sufficient time for gases to escape naturally, thereby locking in defects that ultimately compromise product durability and aesthetic appeal.
How Does Vacuum Die Casting Extract 99.8% of Air from Molten Zinc?
Vacuum-assisted high-pressure die casting fundamentally changes the casting environment by removing air before metal injection occurs. By creating a vacuum of approximately 500mbar within the die cavity, the system eliminates the primary source of porosity—entrapped atmospheric gases—from the equation altogether.
- Vacuum pumps reduce cavity pressure to <50mbar before metal injection
- Real-time pressure monitoring systems ensure consistent vacuum levels
- Specially designed vacuum valves prevent backflow during high-pressure fill
- Complete air extraction cycle takes only 0.8 seconds, maintaining production efficiency
Furthermore, the vacuum system works in harmony with modified gating designs that feature larger runners and sequential fill patterns. These engineering improvements allow molten zinc to flow more laminar (less turbulent) through the mold, significantly decreasing gas entrapment risks. Case studies from leading coffee machine manufacturers demonstrate that implementing reducing porosity from 2% to 0.5% in die casting translates to higher plating yields and superior product quality that consumers can feel in their daily coffee ritual.
What Role Does Mold Flow Analysis Play in Gate Design Success?
Before a single drop of molten zinc enters the die, advanced computer simulation now allows engineers to visualize and optimize metal flow patterns. Mold flow analysis for gate design optimization specifically targets turbulence reduction and uniform cavity filling—two critical factors that directly impact porosity levels in finished coffee machine handles.
- Computational fluid dynamics models predict problematic air traps before production
- Gate redesigns reduce metal velocity from typical 60m/s down to <50m/s
- Runner system optimization prevents premature solidification
- Thermal analysis identifies potential cold shut areas where porosity typically forms
Beyond theoretical benefits, practical application of mold flow analysis has delivered measurable improvements across multiple production parameters. By adjusting gate thickness by just 0.5mm and relocating gates to promote laminar flow, manufacturers have witnessed turbulence reduction of up to 40%. Additionally, properly balanced runner systems ensure consistent metal temperature throughout the fill process, eliminating the temperature gradients that cause shrinkage porosity. Notably, 85% of existing tooling can be modified based on mold flow findings without requiring entirely new molds—making this approach both technically sound and economically viable for operations seeking immediate quality improvements.
How Do Real Production Numbers Prove the Value of Porosity Control?
The ultimate test of any manufacturing improvement comes from production line results. In a detailed analysis of 50,000-unit handle production batches, vacuum die casting combined with optimized gating design demonstrated dramatic quality improvements that directly impacted bottom-line results.
- Porosity reduced from 2.1% to 0.5% as verified by X-ray inspection
- Plating yield improvement in zinc die casting from previous industry average of 70% to 98%
- Scrap reduction saved manufacturers approximately $28,000 per month
- ISO 9001-certified zinc die casting services ensured consistency across production runs
When examining the financial implications more closely, the numbers become even more compelling. With traditional casting methods, a typical 50,000-unit monthly production run would generate 15,000 handles with plating defects (assuming 70% yield). At an average unit cost of $1.87 including materials, labor, and overhead, this represents $28,050 in monthly waste. After implementing vacuum die casting and optimized gate design, the same production volume produces just 1,000 defective units—reducing scrap costs to just $1,870 monthly. This $26,180 monthly savings accumulates to $314,160 annually, providing substantial return on the approximately $150,000 investment in vacuum equipment and process development, with complete payback achieved in under 8 months.
Conclusion
The path to defect-free zinc alloy electroplating lies in the systematic control of porosity through vacuum die casting technologies and scientific mold flow analysis. By reducing porosity from 2% to 0.5%, manufacturers not only achieve the aesthetic perfection customers demand but also realize substantial cost savings through improved plating yields of 98%. The investment in advanced casting technologies delivers rapid returns through reduced scrap, fewer customer complaints, and enhanced brand reputation for quality.
For coffee machine manufacturers seeking to elevate their handle quality while reducing production costs, vacuum die casting represents not just an incremental improvement but a fundamental shift in quality capabilities. The combination of 500mbar vacuum systems, computational mold flow analysis, and ISO 9001-certified processes creates a robust production ecosystem where defects become the exception rather than the rule. With porosity reduced to just 0.5% and plating yields reaching 98%, manufacturers can confidently deliver handles that maintain their beautiful finish throughout years of daily use—exactly what conscious consumers expect from premium coffee equipment.
[External Links Recommendation]
[Zinc alloy die casting porosity control][^1]
[Vacuum die casting for coffee machine handles][^2]
[Plating yield improvement in zinc die casting][^3]
[Mold flow analysis for gate design optimization][^4]
[Reducing porosity from 2% to 0.5% in die casting][^5]
[Defect-free zinc alloy electroplating][^6]
---
[^1]: Explore this link to discover effective techniques for controlling porosity in zinc alloy die casting, ensuring high-quality production.
[^2]: Learn how vacuum die casting enhances the quality and durability of coffee machine handles, making them more reliable and efficient.
[^3]: Find out how to optimize plating yield in zinc die casting processes, leading to better product performance and reduced waste.
[^4]: Understanding mold flow analysis can significantly enhance your design process, ensuring optimal gate placement and improved product quality.
[^5]: Exploring methods to reduce porosity can lead to better casting quality and performance, crucial for manufacturing excellence.
[^6]: Learning about defect-free electroplating techniques can enhance your production processes and product durability.