What Makes Sheet Metal Fabrication Essential in Automotive Production?
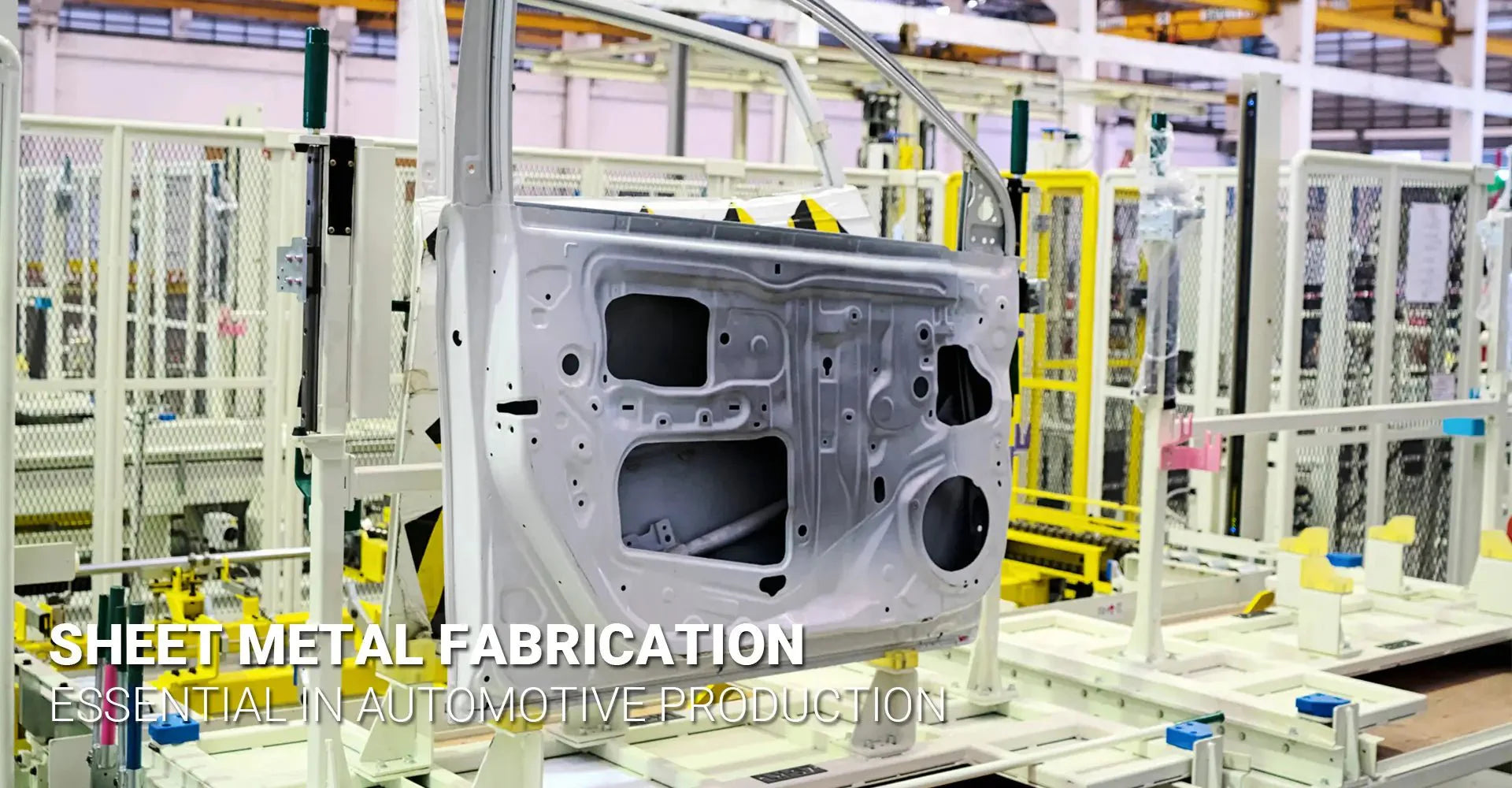
What Makes Sheet Metal Fabrication Essential in Automotive Production?

The global sheet metal fabrication market for automotive reached an impressive $90.23 billion in 2023, highlighting its crucial role in vehicle production. As a cornerstone of the automotive industry, sheet metal fabrication combines precision engineering with cost-effective production methods to create essential vehicle components.
Success in modern automotive production heavily relies on sheet metal fabrication expertise. This process enables manufacturers to produce everything from body panels to structural components, delivering the perfect balance of strength, weight, and durability. With a projected market growth rate of 5.26% CAGR, sheet metal fabrication continues to evolve alongside automotive innovation.
Let's explore how sheet metal fabrication shapes today's vehicles, from material selection to final assembly, and why it remains indispensable in automotive manufacturing.
[Table of Contents]
- How Does Sheet Metal Selection Affect Vehicle Performance?
- Which Sheet Metal Cutting Methods Deliver the Best Results?
- What Role Does Sheet Metal Play in Vehicle Weight Reduction?
- How Do Sheet Metal Components Improve Vehicle Safety?
How Does Sheet Metal Selection Affect Vehicle Performance?
The choice of sheet metal materials directly influences a vehicle's performance, efficiency, and longevity. Modern automotive production relies on a carefully selected range of metals and alloys, each serving specific purposes in vehicle design.
Steel remains the backbone of automotive sheet metal applications, offering exceptional strength and cost-effectiveness. However, aluminum has gained significant traction, particularly in premium vehicles, thanks to its impressive strength-to-weight ratio. Advanced alloys combining multiple metals provide specialized properties for specific components.

The automotive industry's material selection process must balance multiple factors:
- Structural integrity requirements
- Weight reduction goals
- Cost considerations
- Production scalability
- Environmental impact
Which Sheet Metal Cutting Methods Deliver the Best Results?
Modern sheet metal fabrication employs various cutting techniques, each offering unique advantages for automotive applications. Precision and consistency are paramount in producing components that meet strict industry standards.
Laser cutting leads the way in creating complex shapes with exceptional accuracy. This technology allows manufacturers to achieve intricate designs while maintaining tight tolerances. Traditional shear cutting and punching methods continue to prove valuable for specific applications, offering cost-effective solutions for high-volume production.

Expert fabricators combine multiple cutting techniques to optimize production efficiency, minimize material waste, and ensure consistent quality across all components.
What Role Does Sheet Metal Play in Vehicle Weight Reduction?
Weight reduction stands as a primary concern in modern vehicle design, directly impacting fuel efficiency and performance. Strategic use of sheet metal contributes significantly to achieving weight reduction goals without compromising structural integrity.
Through innovative designs and material choices, manufacturers can reduce vehicle weight while maintaining or even improving safety standards. The careful selection of aluminum and high-strength steel allows for thinner components that maintain necessary structural properties.

The surface finish quality of these lightweight components plays a crucial role in both aesthetics and functionality, ensuring proper fit and protection against environmental factors.
How Do Sheet Metal Components Improve Vehicle Safety?
Sheet metal components form the backbone of vehicle safety systems, from crumple zones to reinforced passenger compartments. The strategic design and placement of these components create a protective structure that helps absorb and distribute impact forces.
Quality control in sheet metal fabrication ensures consistent performance across all safety-critical components. Advanced testing methods verify structural integrity, while precise manufacturing processes guarantee reliable performance in real-world conditions.
Manufacturers employ rigorous quality control measures throughout the fabrication process:
- Material composition verification
- Dimensional accuracy checks
- Structural integrity testing
- Surface finish inspection
- Assembly quality validation
Conclusion
Sheet metal fabrication remains fundamental to automotive production, with market projections reaching $143.04 billion by 2032. This growth reflects the industry's continued reliance on sheet metal components for building safer, more efficient vehicles.
The intersection of advanced materials, precision manufacturing, and quality control ensures that sheet metal fabrication will continue meeting the automotive industry's evolving needs. As vehicles become more sophisticated, the role of expert sheet metal fabrication grows increasingly vital.
[External Links]
[sheet metal fabrication technology](https://aminds.com/7-emerging-trends-and-technologies-in-metal-fabrication/)[^1]
[automotive sheet metal fabrication](https://www.worthyhardware.com/news/automotive-sheet-metal-fabrication/)[^2]
[laser cutting](https://www.xometry.com/resources/sheet/laser-cutting-advantages/)[^3]
---
[^1]: Explore this link to discover cutting-edge techniques and innovations in sheet metal fabrication that can enhance your projects.
[^2]: This resource will provide insights into the trends and technologies shaping automotive sheet metal fabrication, crucial for industry professionals.
[^3]: Learn about the advantages of laser cutting technology, which can significantly improve precision and efficiency in manufacturing processes.
-
Posted in
Automotive Parts, Sheet Metal Fabrication