How Can CNC Milling Improve Your Mass Production Efficiency?
- Posted by leeDelsy
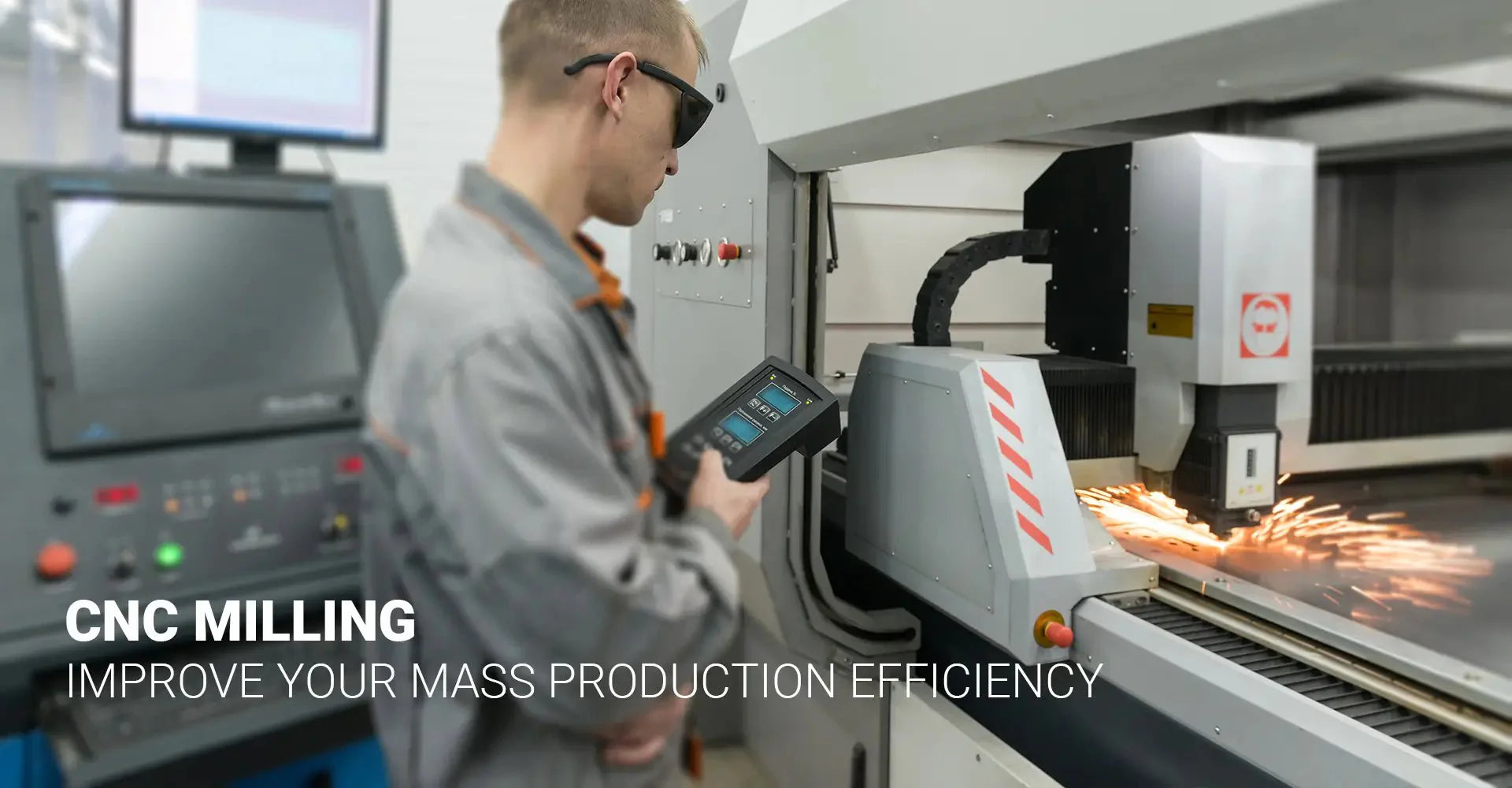
How Can CNC Milling Improve Your Mass Production Efficiency?
In today's competitive manufacturing landscape, finding the most efficient production method is crucial for businesses of all sizes. CNC milling has become a cornerstone technology for mass production across various industries. With its combination of precision, versatility, and automation capabilities, CNC milling offers significant advantages that can transform your manufacturing process and boost your bottom line.
Key Takeaway: CNC milling can improve mass production efficiency by up to 45% compared to traditional manufacturing methods, with market projections showing growth from $81.8 billion in 2024 to $104.3 billion by 2031. The technology delivers consistent part quality, reduces labor costs, and accommodates a wide range of materials—making it ideal for high-volume manufacturing needs.
Whether you're in automotive, aerospace, electronics, or medical device manufacturing, understanding how CNC milling can benefit your specific mass production requirements is essential. Let's explore the specific advantages, cost considerations, material capabilities, and operational variations that make CNC milling such a powerful solution for high-volume manufacturing.
Table of Contents
- What Makes CNC Milling Ideal for High-Volume Manufacturing?
- What Are the Cost Benefits of CNC Milling in Mass Production?
- Which Materials Work Best with CNC Milling for Large-Scale Projects?
- How Do CNC Milling Operations Differ for Various Production Needs?
- Conclusion
What Makes CNC Milling Ideal for High-Volume Manufacturing?
CNC milling excels in mass production environments primarily due to its exceptional precision and consistency. Unlike traditional manufacturing methods, CNC milling services employ computer-controlled machines that execute identical operations with tolerances as tight as +/- 0.0005 inches. This level of accuracy ensures that the thousandth part matches the first in every measurable way—a critical factor for industries where component consistency directly impacts product performance and reliability.
Quick Facts:
- CNC milling machines maintain consistent tolerances between +/- 0.001 in. to +/- 0.005 in. during continuous operation
- Automated programming allows for 24/7 production capabilities, increasing output by up to 40%
- Integration with robotic systems further enhances efficiency, with some facilities reporting 30% increased throughput
- Modern 5-axis CNC systems reduce setup time by 60% compared to traditional milling methods
The automation capabilities of CNC milling deliver substantial advantages for mass production beyond just precision. Furthermore, these systems can be easily programmed to switch between different parts as production needs change, reducing downtime between batches. Additionally, many modern CNC mills incorporate in-process measurement systems that continuously monitor part quality, allowing for immediate adjustments if any deviations are detected. Therefore, this self-correcting capability ensures consistency across production runs that may last weeks or months. Meanwhile, the high repeatability factor makes CNC milling particularly valuable for industries like automotive and aerospace, where component failure could have catastrophic consequences. Because of these advantages, manufacturers can confidently scale production while maintaining stringent quality standards.
What Are the Cost Benefits of CNC Milling in Mass Production?
When evaluating manufacturing methods for mass production, cost considerations inevitably top the list of priorities. CNC milling offers several significant financial advantages that make it particularly attractive for high-volume manufacturing. Initially, the upfront investment in CNC equipment may seem substantial, but the long-term cost benefits become increasingly evident as production scales up. Most importantly, these economic advantages derive from multiple factors that collectively improve the cost-effectiveness of manufacturing operations.
Cost Comparison Table:
Cost Factor | CNC Milling | Traditional Manufacturing |
---|---|---|
Labor Costs | 40-60% lower | Baseline |
Material Waste | 15-25% less | Baseline |
Production Speed | 35-50% faster | Baseline |
Quality Control | 70% fewer defects | Baseline |
Long-term ROI | 15-25% higher | Baseline |
Labor cost reduction represents one of the most significant economic benefits of CNC milling for mass production. Since a single operator can simultaneously monitor multiple CNC machines, the per-part labor cost decreases dramatically as production volume increases. Moreover, the high precision of CNC milling substantially reduces material waste, with computer-optimized cutting paths maximizing the number of parts from raw material. Consequently, this efficiency becomes particularly valuable when working with expensive materials like titanium or specialized alloys. Additionally, the faster production speeds translate directly to improved cash flow, as orders are fulfilled more quickly and production capacity increases. Therefore, businesses utilizing CNC milling can often accept larger orders or shorter deadlines than competitors using traditional methods. Finally, the dramatically lower defect rate means less scrapped material and fewer customer returns, protecting both profit margins and brand reputation.
Which Materials Work Best with CNC Milling for Large-Scale Projects?
Material selection plays a crucial role in determining the success of mass production CNC milling projects. Different materials offer varying combinations of properties—such as strength, machinability, cost, and surface finish quality—that impact both manufacturing efficiency and final product performance. Fortunately, modern CNC milling technology accommodates an impressive range of materials, from common metals to specialized engineering plastics and exotic alloys. This versatility enables manufacturers to select the optimal material for their specific application requirements.
Top Materials for CNC Milling Mass Production:
- Aluminum alloys: Excellent machinability, lightweight, good strength-to-weight ratio, ideal for aerospace and automotive components
- Carbon steel: Versatile, cost-effective, suitable for high-volume components requiring moderate strength
- Stainless steel: Superior corrosion resistance, ideal for medical, food processing, and marine applications
- Engineered plastics: Cost-effective, lightweight alternatives for non-structural components
- Brass and copper alloys: Excellent electrical conductivity, good machinability, perfect for electrical components
- Titanium: Superior strength-to-weight ratio for critical aerospace and medical applications
When selecting materials for mass production via CNC milling, several factors require careful consideration. First, material hardness directly impacts tool wear and machining time—softer materials generally allow for faster cutting speeds and longer tool life, reducing production costs. However, these materials may not provide the mechanical properties needed for demanding applications. Additionally, dimensional stability during machining is critical, especially for precision components. Some materials experience significant thermal expansion during high-speed machining, necessitating specialized cooling strategies or compensation techniques. Moreover, material cost becomes increasingly significant in mass production scenarios, making material efficiency paramount. Therefore, working with experienced CNC machining services that understand these material-specific challenges can help optimize material selection based on both manufacturing requirements and end-use performance needs.
How Do CNC Milling Operations Differ for Various Production Needs?
CNC milling encompasses a diverse range of operations that can be tailored to specific production requirements. Understanding these different milling techniques helps manufacturers select the optimal approach for their particular components and production volumes. Each CNC milling operation offers distinct advantages for specific part geometries, surface finish requirements, and production efficiency considerations. By matching the right milling operation to your production needs, you can maximize efficiency while maintaining quality standards.
Common CNC Milling Operations for Mass Production:
- Face Milling: Creates flat surfaces quickly and efficiently; ideal for high-volume parts requiring precise flat surfaces
- Profile Milling: Generates external contours and shapes; excellent for complex geometries
- Pocket Milling: Removes material from internal areas; perfect for weight reduction in aerospace components
- Gang Milling: Uses multiple cutters simultaneously; increases productivity for mass production of identical parts
- High-Speed Milling: Utilizes increased spindle speeds and specialized toolpaths; reduces cycle times by up to 70%
- 5-Axis Milling: Enables complex geometries in a single setup; reduces handling and improves accuracy
The selection of appropriate CNC milling operations fundamentally impacts production efficiency, especially at scale. For instance, high-speed milling significantly reduces cycle times for suitable materials but requires specialized tooling and machine capabilities to implement effectively. Similarly, 5-axis milling can dramatically reduce setup time and improve accuracy for complex components, though the equipment investment is substantially higher than 3-axis alternatives. Meanwhile, operations like gang milling—where multiple cutters work simultaneously—can boost productivity for simple parts produced in very high volumes. Furthermore, specialized techniques like trochoidal milling extend tool life when working with hardened materials, reducing consumable costs in long production runs. Additionally, the advent of hybrid machining approaches, combining traditional milling with processes like additive manufacturing, opens new possibilities for component design and production efficiency. Consequently, partnering with specialized CNC service providers who understand these operational nuances can help identify the optimal approach for specific mass production needs.
Conclusion
The implementation of CNC milling for mass production offers manufacturers numerous advantages that directly impact efficiency, quality, and bottom-line performance. By leveraging the precision, automation, and versatility inherent in modern CNC technology, businesses can achieve higher production volumes while maintaining exacting quality standards. The continued growth of the CNC milling market—projected to reach $104.3 billion by 2031—underscores the technology's increasing importance in global manufacturing operations.
Throughout this article, we've explored several critical aspects of CNC milling for mass production. First, the precision and automation capabilities make CNC milling uniquely suited for high-volume manufacturing across diverse industries. Second, the cost benefits—including reduced labor expenses, decreased material waste, and improved production speed—contribute to higher returns on investment. Third, material versatility allows manufacturers to select optimal materials based on specific application requirements and cost considerations. Finally, the variety of milling operations enables customization of the manufacturing process to meet particular production needs. By understanding and applying these concepts, manufacturers can make informed decisions about implementing CNC milling to enhance their mass production capabilities.
External Links Recommendation
[High Speed CNC Milling](https://www.americanmicroinc.com/resources/high-speed-cnc-machining-techniques-benefits/)[^1]
[5-Axis milling](https://5-axis.org/)[^2]
[CNC Milling Mass Production](https://fadal.com/benefits-of-cnc-machining-for-manufacturing/)[^3]
[Pocket milling](https://bobcad.com/cnc-software-what-is-pocket-milling/?srsltid=AfmBOorbDWllpD0XFO270OaldE4NcpqSDVqyAUmF8Ljczp2D02RRBiXy)[^4]
[Face Milling](https://waykenrm.com/blogs/what-is-face-milling/)[^5]
---
[^1]: Discover the advantages of High Speed CNC Milling, including faster production times and improved surface finishes.
[^2]: Learn how 5-Axis milling expands machining capabilities, allowing for complex geometries and reduced setup times.
[^3]: Explore this link to understand how CNC milling enhances efficiency and precision in mass production processes.
[^4]: Learn about pocket milling techniques and their applications in CNC machining for better design and manufacturing outcomes.
[^5: Discover the advantages of face milling and how it can improve surface finish and dimensional accuracy in machining.
-
Posted in
CNC milling
- 3D Printing
- 5 Axis CNC Machining
- aluminum die casting
- Automotive Parts
- CAD CAM Software
- CNC lathe
- CNC machining
- CNC Machining Design Guide
- CNC Metal
- CNC milling
- CNC turning
- Coffee grinder burr
- Composite Materials
- consumer electronics manufacturing
- Custom CNC machining Cost
- die casting
- EDM
- End Milling
- high pressure die casting
- High Speed CNC Milling
- high speed machining
- Industrial 3D Printing Machines
- Injection molding
- Kitchen appliances Manufacturing
- low pressure die casting
- On-demand Manufacturing
- Precision Machining
- Rapid Prototype
- Sheet Metal Fabrication
- surface finish
- surface roughness