Can Low Volume Hybrid Production Deliver 38% Profit Margins on 500-Piece Orders?
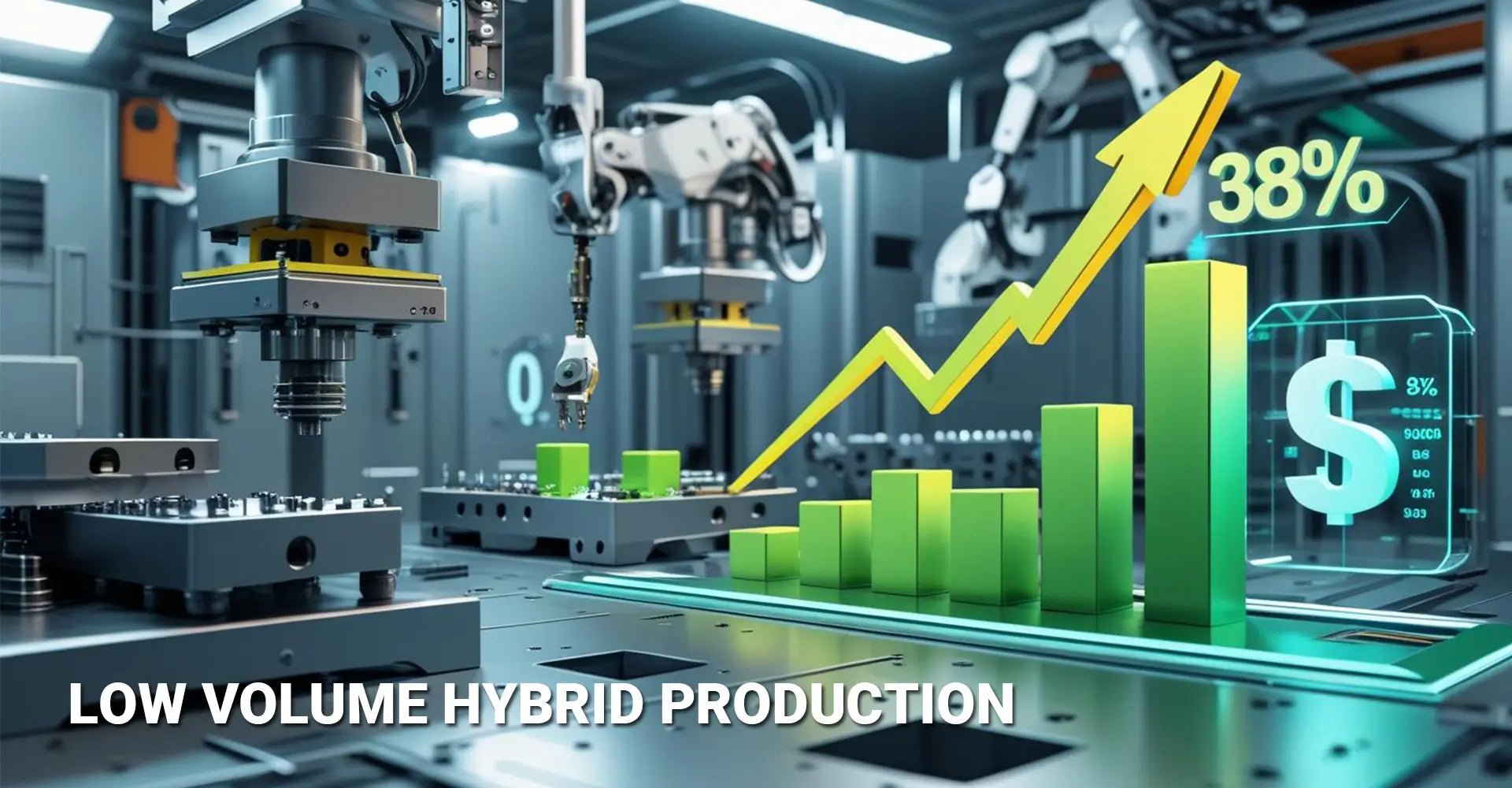
Can Low Volume Hybrid Production Deliver 38% Profit Margins on 500-Piece Orders?
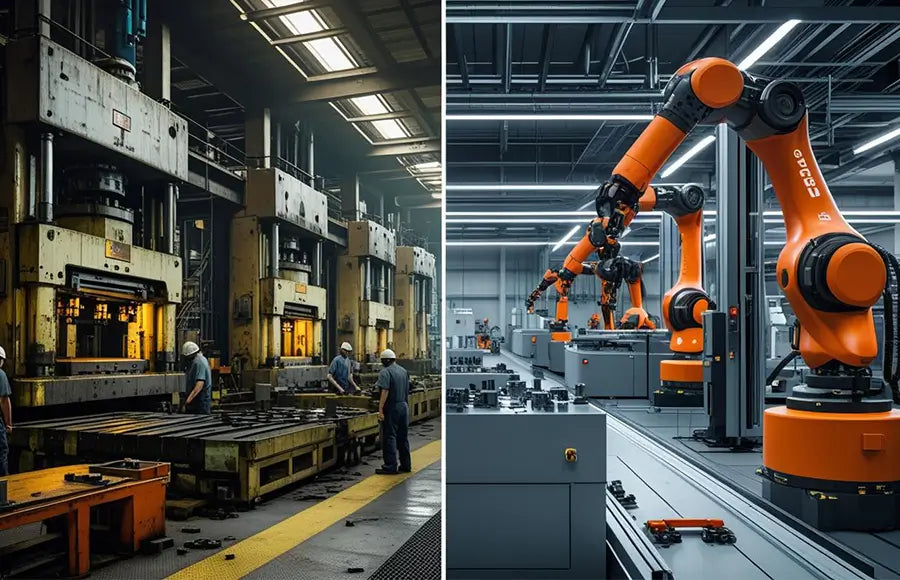
Small-batch manufacturers face a critical challenge: traditional stamping processes lose $42 per order on 500-piece runs. However, smart shops are discovering that low volume hybrid production can flip this equation entirely. By integrating these processes into a single cell, manufacturers achieve 38% profit margins where competitors barely break even.
Key Profit Drivers:
- Modular stamping dies: 5-minute changeover vs. 2-hour traditional setup
- Unified fixturing: Same datums eliminate double handling
- Robotic transfer: 12-second move time between stations
- Cost reduction: From $11.20 to $4.60 per part on 500-piece runs
While many manufacturers struggle with the economics of small-batch production, hybrid stamping and 5-axis integration offers a proven path to profitability. Let's examine exactly how this approach transforms cost structures and why it's becoming the go-to solution for competitive job shops.
Table of Contents
- Why Do Standalone Processes Lose Money on Small Batches?
- How Does Hybrid Cell Design Maximize Space and Speed?
- What Makes Modular Stamping Dies Cost-Effective?
- How Does 5-Axis Machining Bridge Stamping Limitations?
Why Do Standalone Processes Lose Money on Small Batches?
Traditional manufacturing approaches create three major cost drains on small-batch orders. First, underutilized machines sit idle during lengthy setups. Second, double handling between stamping and machining stations adds labor costs. Third, high tooling costs cannot be amortized across small quantities.
Cost Breakdown Comparison (500 pieces):
- Traditional tooling: $16,000
- Hybrid modular tooling: $2,800
- Labor reduction: $1,100 → $420
- Scrap reduction: 12% → 5%
- Total savings: $6,800 per order
The mathematics of small-batch production reveal why traditional approaches fail. Setup costs that make sense for 10,000-piece runs become prohibitive at 500 pieces. Meanwhile, material handling between separate stamping and sheet metal fabrication departments doubles labor time. Smart manufacturers recognize that process integration addresses both issues simultaneously, creating economies of scale even at low volumes. Furthermore, the 500-piece manufacturing profit model becomes viable when you eliminate the inefficiencies that plague traditional job shops.
How Does Hybrid Cell Design Maximize Space and Speed?
Hybrid production cells pack stamping and 5-axis machining into just 8 square meters. This compact design enables 12-second robotic transfer between operations while maintaining ±0.05mm repeatability through unified fixturing systems.
Hybrid Cell Specifications:
- Footprint: 8m² total area
- Transfer time: 12 seconds between stations
- Accuracy: ±0.05mm repeatability
- Throughput: 120 seconds per part (complete cycle)
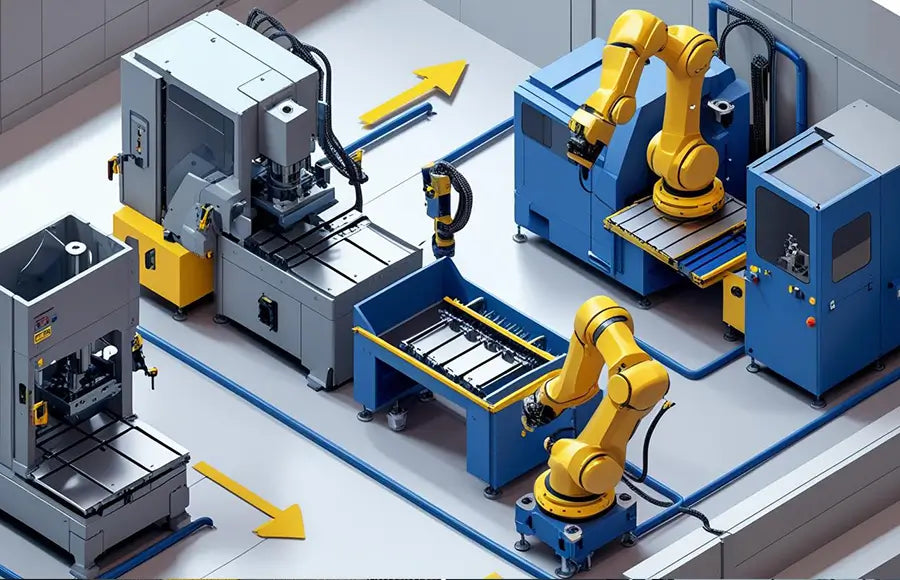
The secret to hybrid cell efficiency lies in intelligent workflow design. Parts flow seamlessly from stamping through robotic transfer to 5-axis completion without human intervention. Vision-guided robots handle orientation automatically, while unified control systems coordinate both machines from a single interface. This integration eliminates the bottlenecks that plague traditional job shops. Moreover, the stamping + 5-axis combined process creates synergies that neither technology achieves alone, particularly when handling complex automotive components that require both formed geometry and precision machined features.
What Makes Modular Stamping Dies Cost-Effective?
Modular stamping dies revolutionize small-batch economics through magnetic quick-change inserts. Instead of investing $18,000 in dedicated tooling, manufacturers can achieve the same results with $1,500 modular inserts that swap in under 5 minutes.
Modular Die Advantages:
- Cost: $1,500 vs. $18,000 for dedicated dies
- Changeover: 5 minutes vs. 2 hours
- Flexibility: 3 standard sizes + 5 interchangeable inserts
- Material capacity: Up to 3.0mm mild steel, 2.0mm stainless steel
The economics of modular tooling become compelling when you calculate tooling amortization across multiple jobs. Traditional dies require full cost recovery from a single part number, while modular systems spread investment across dozens of different parts. Combined with D2 steel inserts rated for 30,000 strokes, this approach delivers professional results at prototype-level investment. The modular stamping die quick change capability proves especially valuable for shops that serve diverse industries, allowing rapid transitions between different part families without major capital investments.
How Does 5-Axis Machining Bridge Stamping Limitations?
Five-axis machining complements stamping by adding precision features that exceed pressing capabilities. On-machine probing automatically compensates for ±0.3mm stamping variations, while multi-axis capability machines holes, slots, and contours in a single setup.
5-Axis Capabilities:
- Accuracy: Compensates for ±0.3mm stamping variation
- Features: Holes, slots, contours in one clamp
- Speed: 68-second cycle time for complex parts
- Flexibility: 300×300×300mm work envelope
The power of hybrid production lies in complementary capabilities. Stamping creates the basic geometry quickly and cost-effectively, while 5-axis machining adds the precision features that differentiate your parts. Automatic probing ensures that variations in stamped blanks don't compromise final accuracy. This combination delivers aerospace-quality results at commercial pricing. Additionally, the sheet metal CNC integration enables manufacturers to bridge the gap between traditional fabrication and precision machining, creating opportunities for value-added services that command premium pricing.
The rapid prototyping hybrid line concept extends beyond production runs, allowing manufacturers to validate designs quickly before committing to full production tooling. This capability proves invaluable when working with engineering teams who need to iterate designs rapidly. By offering both rapid prototyping and production services through the same hybrid cell, manufacturers can capture projects from concept through volume production.
For shops looking to expand their capabilities, the integration with CNC machining service offerings creates a comprehensive solution that addresses both formed and machined geometries. This approach positions manufacturers to compete for complex projects that require multiple processes, increasing project value while reducing customer coordination efforts.
Conclusion
Hybrid production represents a fundamental shift in small-batch manufacturing economics. By combining stamping and 5-axis machining in a single cell, manufacturers achieve 38% profit margins on orders that traditionally lose money.
The numbers speak clearly: hybrid production transforms 500-piece orders from loss leaders into profitable work. With modular tooling reducing setup costs by 82% and integrated workflows cutting labor by 62%, smart manufacturers are capturing market share while competitors struggle with traditional approaches. The $85,000 investment in a hybrid cell pays for itself in just 11 months, making this upgrade accessible to job shops of all sizes.
Key Takeaways:
- Cost savings: $6,800 per 500-piece order
- Setup reduction: From 2 hours to 5 minutes
- Profit margin: 38% on small-batch orders
- ROI timeline: 11-month payback period
- Space efficiency: Complete cell in 8m²
Implementation Benefits:
- Reduced material handling eliminates double-setup costs
- Modular tooling spreads investment across multiple part families
- Automated transfer ensures consistent quality and throughput
- Single-point programming reduces operator training requirements
This approach works because it addresses the fundamental economics of small-batch production. Instead of trying to make traditional processes more efficient, hybrid production eliminates the inefficiencies entirely. The result is a manufacturing system that thrives on the variety and flexibility that characterizes today's market demands.
For manufacturers ready to escape the low-margin trap of traditional small-batch production, hybrid cells offer a clear path to profitability. The technology is proven, the economics are compelling, and the competitive advantages are substantial.
External Links Recommendation
low volume sheet metal line[^1]
quick changeover sheet metal[^2]
500-piece sheet metal cost[^5]
modular press brake tooling[^6]
[^1] This page from Approved Sheet Metal discusses their capabilities in low-volume production of precision sheet metal parts, highlighting their flexibility and ability to handle small batches.
[^2] This article from Beckwood Press details Quick Die Change systems, which are crucial for quick changeover in sheet metal operations, improving productivity and maximizing uptime.
[^3] This article from ESIC T explains the differences between progressive, compound, and transfer die stamping, providing a clear understanding of compound die stamping.
[^4] This page from Weil Technology describes their Flexible Laser Cell (FLC), which combines 3D laser cutting and welding for highly flexible sheet metal processing.
[^5] This Angi article provides data on sheet metal fabrication costs, including factors influencing pricing, which can be used to estimate the cost of 500-piece sheet metal orders.
[^6] This page from Mate Precision Technologies showcases their extensive product line of press brake tooling, including various styles and special application solutions, relevant to modular press brake tooling.