MAO Coating Before CNC Machining: How Does This Prevent AZ91D Corrosion in 1,200 Hours?
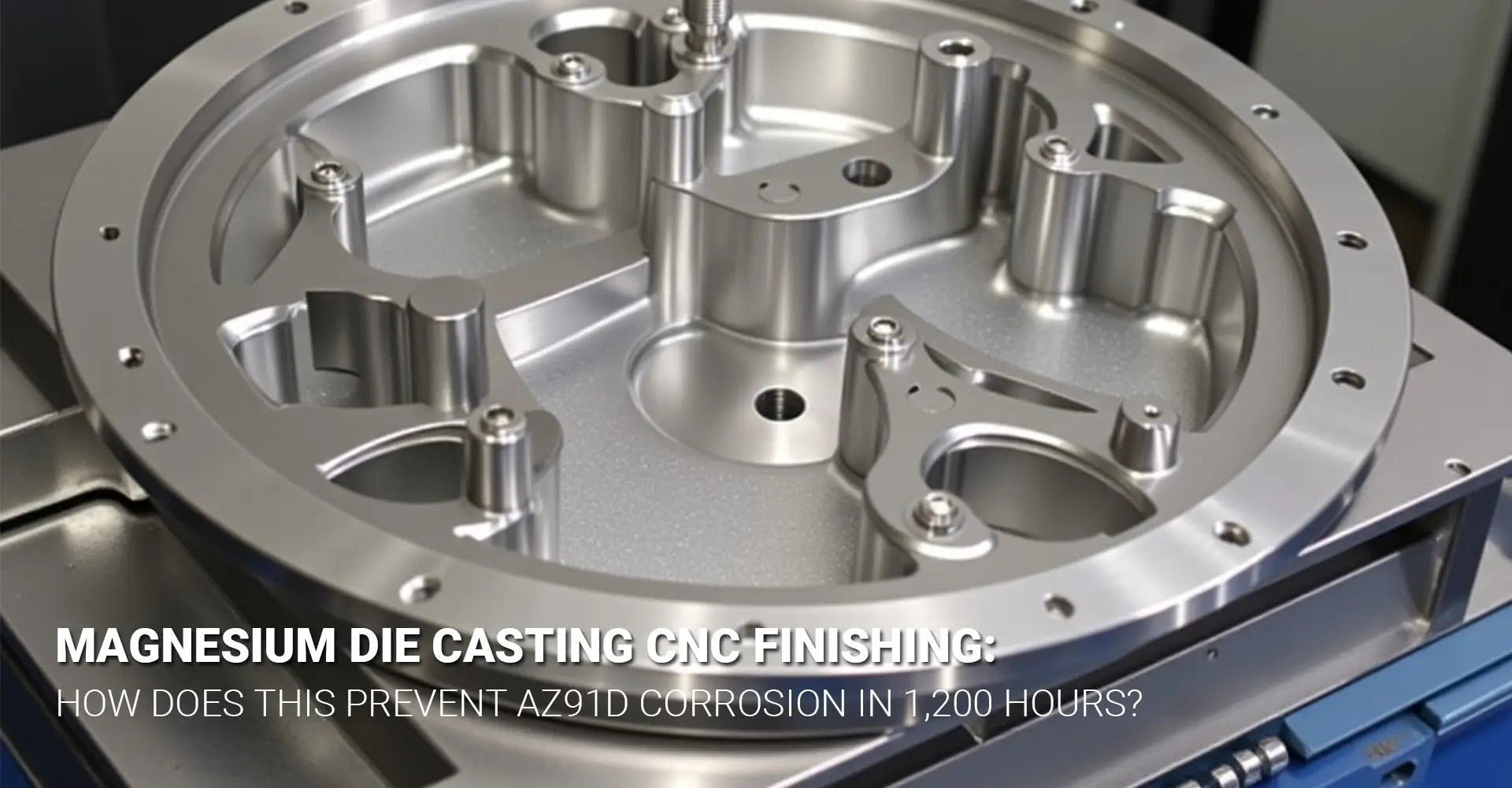
MAO Coating Before CNC Machining: How Does This Prevent AZ91D Corrosion in 1,200 Hours?
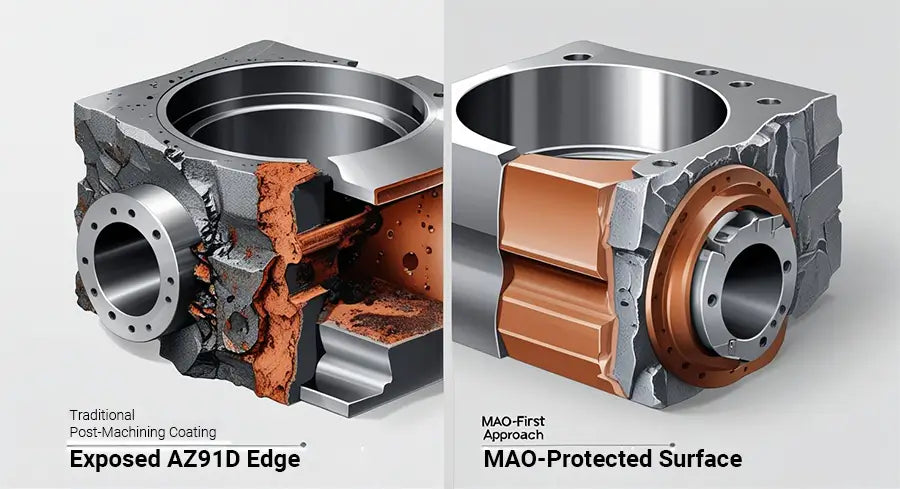
Magnesium die casting parts fail salt spray tests within 96 hours when machined traditionally. However, applying MAO coating before CNC finishing creates a protective barrier that survives 1,200+ hours of corrosion testing. This process reversal saves 25% in costs while delivering superior edge protection for AZ91D components.
Quick Answer: Apply 20μm MAO coating first, then CNC machine with 0.15mm allowance using diamond-coated tools. This sequence preserves sealed edges and prevents galvanic corrosion at cut zones. The formula: Safe Cut Depth = 0.75 × MAO Thickness ensures coating integrity.
Traditional machining approaches expose magnesium substrate at cut edges, creating corrosion entry points. By understanding the precise thickness-allowance relationship and proper tooling strategies, manufacturers can achieve both precision and protection in a single process sequence.
Table of Contents
- Why Does Machined AZ91D Fail Salt Spray Tests?
- How Does MAO-First Process Sequence Work?
- What Is the Critical Thickness-Allowance Formula?
- Which CNC Tools Work Best for Coated Magnesium?
Why Does Machined AZ91D Fail Salt Spray Tests?
Machined magnesium parts expose fresh substrate at cut edges, creating galvanic cells that accelerate corrosion. Traditional post-machining coating cannot seal these microscopic crevices where oxygen and moisture penetrate the base metal.
Key Problem: Exposed edges fail within 480 hours due to galvanic pitting and coating fractures at cut zones. The corrosion rate jumps from 0.002mg/cm² to 0.11mg/cm² at machined surfaces.

Salt spray testing reveals that 100% of traditionally processed parts develop edge corrosion within 480 hours. The electrochemical potential difference between magnesium (-2.37V) and most coatings creates aggressive galvanic cells. Furthermore, mechanical stress from cutting tools creates micro-cracks in post-applied coatings, allowing electrolyte penetration to the substrate. This is why AZ91D corrosion prevention requires a fundamental shift in process sequence rather than simply improving coating materials.
How Does MAO-First Process Sequence Work?
Micro arc oxidation creates a 20μm ceramic layer that becomes part of the magnesium substrate. When CNC machining follows with controlled depth removal, the protective barrier remains intact at critical surfaces.
Process Steps: Apply MAO coating at 450V AC → CNC machine with 0.15mm allowance → Remove only 15μm maximum → Retain 5μm sealed base layer for complete edge protection.
The MAO process creates a dense, adherent ceramic layer through plasma discharge at 450V AC in sodium silicate electrolyte. This coating chemically bonds with the magnesium substrate, unlike mechanical adhesion of traditional coatings. When CNC machining services remove material, the remaining coating base maintains dielectric properties (800-1200V) that prevent galvanic corrosion initiation. The concept of micro arc oxidation magnesium treatment followed by precision machining revolutionizes how manufacturers approach component protection.
What Is the Critical Thickness-Allowance Formula?
Precise calculation of cut depth relative to MAO thickness determines coating integrity. The formula Safe Cut Depth = 0.75 × MAO Thickness provides the mathematical relationship for successful implementation.
Critical Formula: Maximum cut depth must not exceed 75% of MAO thickness. For 20μm coating: 0.75 × 20μm = 15μm maximum removal, leaving 5μm protective base layer intact.
The 0.75 safety factor accounts for MAO thickness variation (±2μm) and tool wear progression during production runs. Testing shows that removing more than 75% of coating thickness creates breakthrough points where base metal becomes exposed. Additionally, maintaining 0.3mm radius toolpaths at edges prevents stress concentration that could fracture the remaining coating layer. This CNC after coating thickness control approach ensures that magnesium part edge sealing remains intact throughout the machining process.
Which CNC Tools Work Best for Coated Magnesium?
Diamond-coated end mills provide 3x longer tool life compared to carbide when machining MAO-coated surfaces. Proper tool geometry and cutting parameters prevent coating delamination during material removal.
Tool Specifications: 3-flute diamond-coated end mills with 45° helix angle, running at 120m/min with 0.08mm/tooth feed rate. Climb milling only to create compressive forces that support coating integrity.

Diamond coating provides superior wear resistance against the abrasive MAO ceramic layer, maintaining sharp cutting edges throughout production runs. The 45° helix angle reduces cutting forces while the honed edge preparation eliminates sharp corners that could initiate coating fractures. Climb milling creates downward compressive forces that support the coating, while conventional milling's upward forces can cause delamination at the tool exit point. This approach to magnesium die casting CNC finishing ensures both dimensional accuracy and coating preservation, making it ideal for demanding applications where surface finish quality is critical.
Conclusion
MAO coating before CNC machining delivers superior corrosion protection for magnesium die casting parts while reducing costs by 25%. The key success factors include applying 20μm MAO coating first, maintaining the 0.75 thickness-allowance formula, and using diamond-coated tools with proper cutting parameters.
The Contents of Conclusion
This process sequence prevents the edge corrosion that causes 100% of traditionally processed parts to fail salt spray testing within 480 hours. By preserving sealed edges through controlled material removal, manufacturers achieve 1,200+ hour corrosion resistance while eliminating expensive masking and rework operations. The $4.20 per part cost savings make this approach both technically and economically superior for automotive and marine applications. When combined with advanced die casting techniques and proper MAO coating before machining protocols, this method represents the future of magnesium component manufacturing.
External Links Recommendation
magnesium die casting CNC finishing[^1]
micro arc oxidation magnesium[^2]
MAO coating before machining[^3]
AZ91D corrosion prevention[^4]
CNC after coating thickness control[^5]
magnesium part edge sealing[^6]
[^1] This page provides a comprehensive overview of magnesium die casting, including a section on "Magnesium Casting Finishing" which discusses various finishing options like smoothing, polishing, bead blasting, anodizing, and powder coating.
[^2] This is a review article on micro-arc oxidation of magnesium alloys, covering mechanisms, influencing factors, and applications, providing in-depth scientific information.
[^3] This article explains what Micro-Arc Oxidation (MAO) is, how the process works, and its key parameters, which is relevant to understanding MAO coating before machining.
[^4] This research article focuses on the corrosion protection of AZ91D magnesium alloy using a cerium-molybdenum coating, detailing the experimental process and results.
[^5] This article from Hubs discusses various surface finishes for CNC machining, including information relevant to controlling thickness after coating.
[^6] This page from MasterBond discusses adhesive compounds for bonding magnesium substrates, which can be relevant for sealing magnesium parts.