How Do Low Volume Sheet Metal Lines Cut Costs by 60% for 500-Piece Orders?

How Do Low Volume Sheet Metal Lines Cut Costs by 60% for 500-Piece Orders?
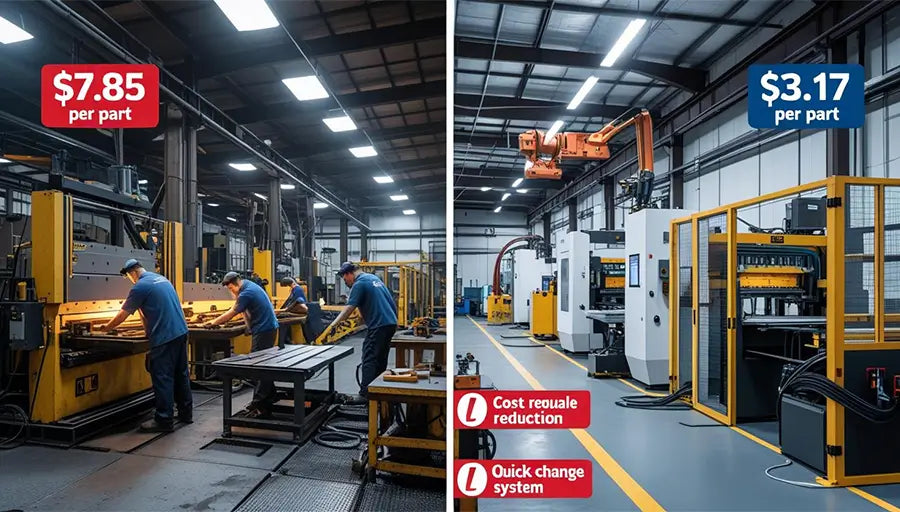
Small batch sheet metal fabrication is bleeding money. Traditional production lines charge $7.85 per part for 500-piece orders, making low volume runs financially painful. However, flexible sheet metal lines slash costs to just $3.17 per part through quick-change systems and compound dies. This means 60% cost reduction that transforms unprofitable small batches into lucrative opportunities.
Quick Facts:
- Cost Reduction: 60% savings ($7.85 → $3.17 per part)
- Setup Time: 90 seconds vs. 45 minutes
- Floor Space: Only 21m² required
- ROI Timeline: 14 months payback
- Batch Size: Profitable at 500 pieces
Traditional sheet metal fabrication treats small batches as necessary evils. Yet, smart manufacturers are discovering that flexible production lines don't just reduce costs—they unlock entirely new revenue streams. Let's explore how this transformation works.
Table of Contents
- Why Do Traditional Sheet Metal Lines Fail at Small Batches?
- What Makes Quick-Change Systems So Powerful?
- How Do Compound Dies Reduce Operations by 70%?
- What Equipment Configuration Delivers Best ROI?
Why Do Traditional Sheet Metal Lines Fail at Small Batches?
Traditional sheet metal production operates on high-volume assumptions. Consequently, setup times dominate costs when batch sizes drop below 2,000 pieces. Moreover, dedicated tooling creates massive upfront investments that small orders cannot justify.
The $220/Hour Problem:
- Setup delays: 45-90 minutes per changeover
- Underutilized presses: 40% downtime during tool changes
- NRE traps: $6,200 tooling costs for 500-piece orders
- Manual handling: 3x labor requirements

Traditional lines suffer from three critical flaws. First, manual tool changes require skilled operators for 45-90 minutes per setup. Second, dedicated tooling costs $6,200-$8,500 per job, crushing profitability on small orders. Third, sequential operations demand multiple machine passes, multiplying handling costs. These factors combine to create the $220/hour cost burden that makes small batches financially toxic.
Furthermore, traditional sheet metal fabrication processes struggle with frequent changeovers. Each setup requires extensive calibration, tooling adjustments, and quality checks. Meanwhile, operators spend valuable time searching for correct tools and programming parameters. The result is a low volume sheet metal line that operates at 40% efficiency, making small orders unprofitable.
What Makes Quick-Change Systems So Powerful?
Quick-change systems eliminate the primary cost driver in small batch production: setup time. Furthermore, magnetic tooling and pre-staged carts reduce tool swaps from 45 minutes to just 90 seconds. This dramatic reduction transforms the economics of low volume manufacturing.
90-Second Tool Swap Process:
- Release: Deactivate electromagnets (5 seconds)
- Swap: Remove and replace tool stack (70 seconds)
- Calibrate: Laser alignment auto-correction (15 seconds)
- Result: 30x faster than manual bolted systems

Magnetic tooling revolutionizes setup procedures through electromagnetic clamping systems. Additionally, laser-coded dies enable automatic program selection via barcode scanning. Pre-staged tool carts eliminate search time, while magnetic release systems require zero bolts or manual fasteners. The result is consistent 90-second changeovers that make small batches as profitable as large runs.
Advanced industrial machinery incorporates sophisticated control systems that streamline operations. Smart sensors detect tool positioning automatically, while programmable logic controllers store hundreds of job parameters. Therefore, quick changeover sheet metal systems eliminate human error and reduce setup variations. Operators simply scan barcodes to load complete job settings, including cutting parameters, bending angles, and quality specifications.
How Do Compound Dies Reduce Operations by 70%?
Compound dies perform multiple operations in a single stroke, dramatically reducing handling and setup costs. Instead of separate punching, flanging, and forming steps, compound dies complete all operations simultaneously. This approach cuts cycle times by 70% while maintaining precision.
Compound Die Advantages:
- Operations: Punch + flange + form in 1 stroke
- Handling: 70% reduction in part transfers
- Tooling Cost: $1,200 modular inserts vs. $8,500 full dies
- Cycle Time: 45 seconds vs. 180 seconds traditional
Compound dies integrate multiple forming operations into single tooling assemblies. Modular inserts cost just $1,200 compared to $8,500 for dedicated full dies. These systems handle up to 2.0mm stainless steel and 3.0mm mild steel with 50,000-stroke tool life. The elimination of part handling between operations reduces labor costs by 70% while improving quality through consistent positioning.
Compound die stamping technology delivers exceptional accuracy through precisely engineered tool geometry. Progressive dies advance parts through multiple stations, while transfer systems move components between operations. However, compound dies surpass both approaches by completing all operations in a single stroke. This eliminates accumulation of tolerances and reduces scrap rates significantly.
Modern rapid prototyping techniques enable precise die design validation before production. Engineers use finite element analysis to predict material flow and stress distribution. Consequently, compound dies achieve first-part accuracy and minimize costly tooling modifications. The result is a flexible sheet metal cell that delivers consistent quality across varying batch sizes.
What Equipment Configuration Delivers Best ROI?
The optimal flexible line configuration requires just three machines in 21m² floor space. This compact layout includes 2kW fiber laser cutting, 80-ton electric press with quick-change tooling, and robotic deburring system. Total investment of $110,200 delivers 14-month ROI at 10 orders per month.
Equipment Breakdown:
- 2kW Fiber Laser: $42,000 (cutting blanks)
- 80t Electric Press: $48,000 (compound dies)
- 6-Axis Robot: $18,000 (deburring + stacking)
- Magnetic Tooling: $2,200 (quick-change system)
- Total Investment: $110,200
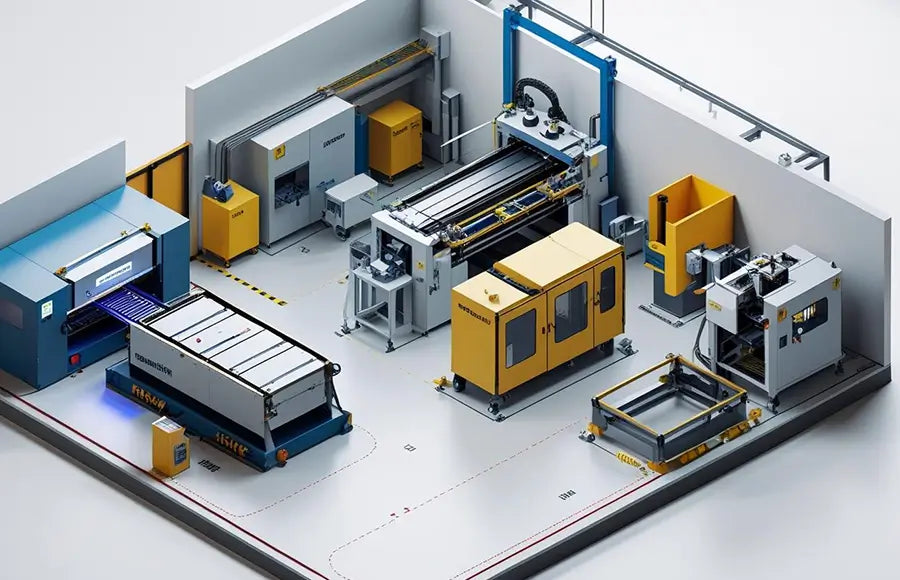
The 6m × 3.5m footprint maximizes productivity per square meter. Fiber laser cutting completes 500 blanks in 6 minutes at 12m/min feed rate. Electric press with compound dies processes parts at 45 strokes per minute. Robotic deburring achieves Ra 1.6μm surface finish in 45 seconds per part. This configuration processes 500-piece orders in 55 minutes compared to 180 minutes for traditional methods.
Material selection plays a crucial role in achieving target economics. Common sheet metals include cold-rolled steel, stainless steel, and aluminum alloys. Each material requires specific cutting parameters and forming considerations. However, flexible lines adapt automatically to different materials through programmable controls.
The 500-piece sheet metal cost calculation depends on several factors. Material costs typically represent 60% of total expenses, while tooling and setup account for 25%. Labor comprises the remaining 15% through reduced handling requirements. Therefore, flexible lines achieve dramatic cost reductions by minimizing setup time and tooling investments.
Modular press brake tooling further enhances flexibility by enabling rapid configuration changes. Standard tool holders accept various punch and die combinations without custom modifications. Moreover, magnetic clamping systems eliminate time-consuming bolt adjustments. The result is a production system that adapts quickly to changing requirements while maintaining consistent quality.
Conclusion
Flexible sheet metal lines transform small batch economics through quick-change systems and compound dies. The 60% cost reduction from $7.85 to $3.17 per part makes 500-piece orders profitable instead of painful.
Smart manufacturers are discovering that flexible production lines don't just reduce costs—they create competitive advantages. Quick-change systems eliminate setup delays, compound dies reduce handling, and compact configurations minimize floor space requirements. With 14-month ROI and 60% cost savings, flexible lines turn small batch challenges into profit opportunities. The question isn't whether to invest in flexible sheet metal technology—it's how quickly you can implement it.
External Links Recommendation
low volume sheet metal line[^1]
quick changeover sheet metal[^2]
500-piece sheet metal cost[^5]
modular press brake tooling[^6]
[^1] This page from Approved Sheet Metal discusses their capabilities in low-volume production of precision sheet metal parts, highlighting their flexibility and ability to handle small batches.
[^2] This article from Beckwood Press details Quick Die Change systems, which are crucial for quick changeover in sheet metal operations, improving productivity and maximizing uptime.
[^3] This article from ESIC T explains the differences between progressive, compound, and transfer die stamping, providing a clear understanding of compound die stamping.
[^4] This page from Weil Technology describes their Flexible Laser Cell (FLC), which combines 3D laser cutting and welding for highly flexible sheet metal processing.
[^5] This Angi article provides data on sheet metal fabrication costs, including factors influencing pricing, which can be used to estimate the cost of 500-piece sheet metal orders.
[^6] This page from Mate Precision Technologies showcases their extensive product line of press brake tooling, including various styles and special application solutions, relevant to modular press brake tooling.