Why Do EV Battery Housings Fail Leak Tests at 92% Yield?
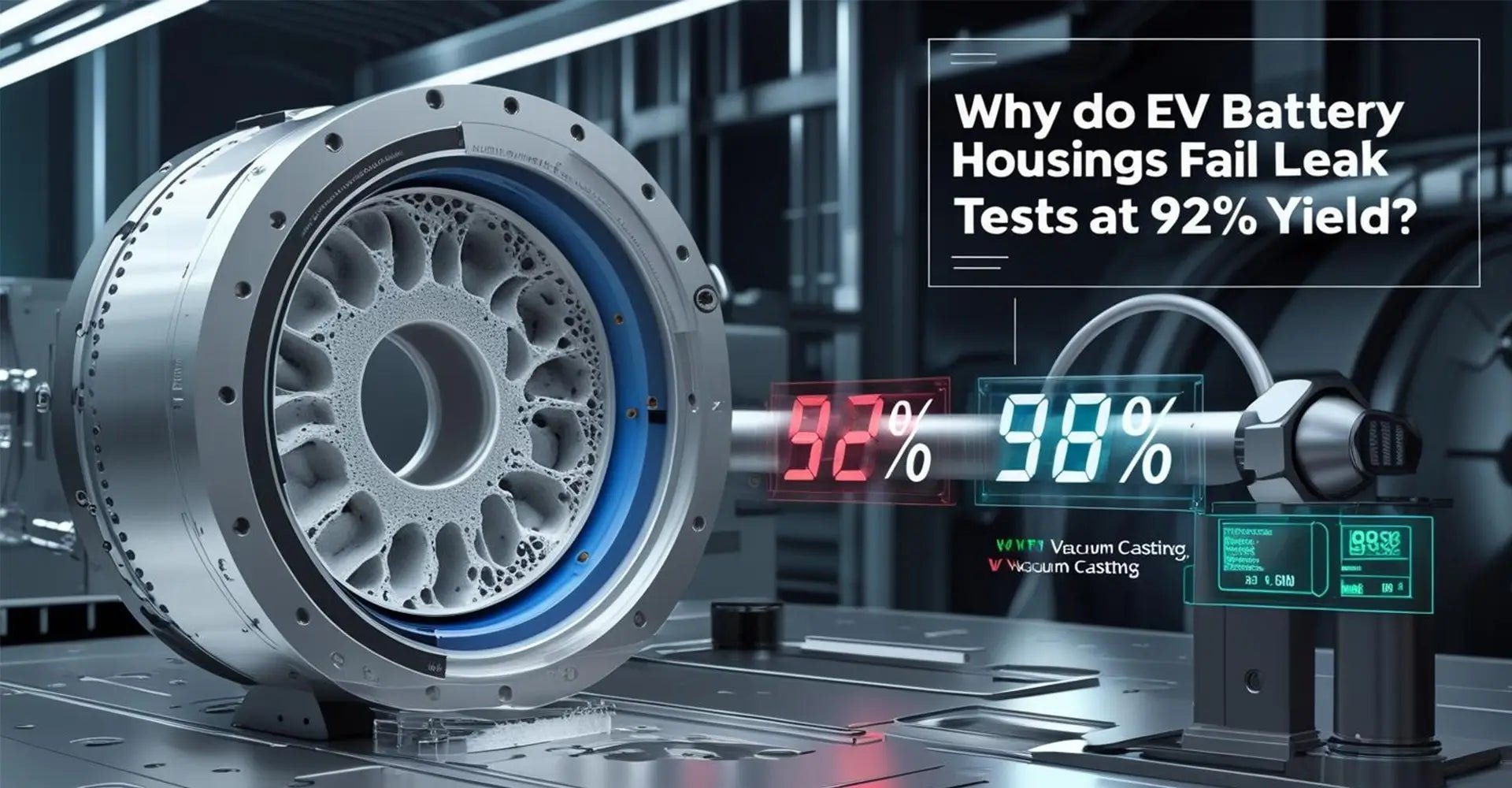
Why Do EV Battery Housings Fail Leak Tests at 92% Yield?

EV manufacturers lose $42 per housing due to porosity defects that cause leak test failures. Standard die casting achieves only 92% yield, while vacuum-assisted methods reach 98% yield by maintaining ≤80mbar pressure during casting. This significant difference directly impacts production costs and quality standards across the automotive industry.
Quick Answer: The Solution at a Glance
Key Success Factors:
- Vacuum level: ≤80mbar (reduces porosity from 1.8% to 0.12%)
- Topology-optimized venting: 37% faster air evacuation
- Process timing: 0.3s vacuum delay after metal injection
- ROI: $18k vacuum upgrade pays back in 4 months
Understanding the science behind vacuum die casting porosity control helps manufacturers avoid costly defects. Meanwhile, this approach ensures compliance with stringent EV safety standards while maintaining profitable production rates.
Table of Contents
- What Causes Porosity Problems in EV Battery Housings?
- How Does 80mbar Vacuum Pressure Reduce Casting Defects?
- Why Do Topology-Optimized Vents Work Better Than Traditional Slots?
- What Are the Critical Process Parameters for 98% Yield?
What Causes Porosity Problems in EV Battery Housings?
Trapped air creates weak spots in aluminum die castings, especially in complex EV battery housings where crash safety depends on structural integrity. These defects occur when molten metal flows through intricate geometries at high speeds. Furthermore, traditional die casting methods struggle with complete air evacuation in complex parts.
The Impact of Porosity on Production Quality
Porosity Impact Data:
- Standard process: 1.8% porosity, 89.5% leak test pass rate
- Vacuum process: 0.12% porosity, 99.2% leak test pass rate
- Tensile strength increase: 240 MPa → 290 MPa

Air entrapment occurs when molten aluminum flows rapidly through complex geometries, creating turbulence that traps gas bubbles. These micro-voids weaken the casting structure and cause blistering during leak testing. Furthermore, trapped air prevents proper metal flow, resulting in incomplete fill patterns that compromise crash zone performance. The vacuum die casting porosity EV challenge requires precise control of multiple variables to achieve consistent results.
How Does 80mbar Vacuum Pressure Reduce Casting Defects?
Vacuum pressure below 80mbar creates the ideal environment for air evacuation without compromising metal flow velocity or cycle time. This pressure threshold represents a critical balance between effective degassing and maintaining production efficiency. Additionally, 80mbar vacuum die casting achieves superior results compared to higher pressure levels.
Performance Data by Vacuum Level
Vacuum Level Performance:
Vacuum Level | Porosity % | Leak Test Pass Rate |
---|---|---|
500mbar | 2.8% | 85% |
200mbar | 1.5% | 92% |
80mbar | 0.12% | 99.2% |
The 80mbar threshold represents the point where gas solubility in molten aluminum drops significantly, preventing bubble formation during solidification. Additionally, this vacuum level maintains proper metal injection velocity while allowing sufficient time for air evacuation through optimized vent channels. Real-time pressure monitoring ensures consistent vacuum levels throughout the casting cycle. Modern automotive manufacturing demands this level of precision to meet safety standards.
Why Do Topology-Optimized Vents Work Better Than Traditional Slots?
Computer-aided vent design identifies exact air trap locations and creates three-dimensional evacuation paths that traditional straight slots cannot match. This approach uses advanced software to simulate air flow patterns during die filling. Moreover, mold venting topology optimization delivers measurable improvements in air evacuation efficiency.
Comparing Venting Technologies
Venting Comparison:
- Traditional slots: 0.5mm width, straight channels
- Topology-optimized: 0.15mm micro-vents + 1mm collector channels
- Air evacuation speed: 37% faster with optimized design

CFD analysis reveals that air flows in complex three-dimensional patterns during die filling, requiring curved vent paths that follow natural air movement. Micro-vents at 0.15mm width allow air escape while preventing metal breakthrough, while collector channels gather evacuated air efficiently. This design approach reduces vent clogging and maintains consistent performance across production runs. EV battery housing porosity issues decrease significantly when manufacturers implement these advanced venting strategies.
What Are the Critical Process Parameters for 98% Yield?
Achieving consistent 98% yield requires precise control of vacuum timing, pressure levels, and metal solidification parameters. Each parameter works together to create optimal casting conditions. Therefore, high integrity die casting depends on maintaining strict process control throughout production.
Essential Process Control Parameters
Critical Parameters:
- Vacuum delay: 0.3s after metal injection
- Hold pressure: 500 bar for 8 seconds
- Injection speed: 4.5 m/s for turbulence control
- Cycle time increase: Only 3-5 seconds
The 0.3-second vacuum delay prevents metal from being drawn into vent channels while ensuring complete cavity filling before air evacuation begins. High hold pressure at 500 bar compresses any remaining micro-pores during solidification, while controlled injection speed minimizes turbulence-induced air entrapment. These parameters work together to maintain production efficiency while dramatically improving casting quality. Proper vacuum valve placement die configuration ensures consistent performance across multiple production cycles. Secondary operations like CNC machining benefit from higher quality castings with reduced porosity. Additionally, various metals and plastics require similar attention to process control for optimal results.
Conclusion
Vacuum die casting porosity control transforms EV battery housing production from 92% to 98% yield through precise pressure management and advanced venting design.
Manufacturing success depends on implementing three key elements: maintaining ≤80mbar vacuum pressure, using topology-optimized venting, and controlling process timing. The $18k investment in vacuum equipment pays for itself within four months through reduced scrap rates and improved leak test performance. EV manufacturers can achieve both quality and profitability targets by following these proven vacuum die casting principles. Therefore, companies that adopt these methods gain competitive advantages in the rapidly growing electric vehicle market.
External Links Recommendation
vacuum die casting porosity EV[^1]
mold venting topology optimization[^3]
EV battery housing porosity[^4]
high integrity die casting[^5]
vacuum valve placement die[^6]
[^1] This article discusses how eliminating porosity in die-cast parts through vacuum impregnation can help cut weight in EVs, making it relevant to vacuum die casting porosity in EVs.
[^2] This Vormetal article explains vacuum-assisted high-pressure die casting, including details on vacuum levels like 80mbar, and its benefits in reducing porosity.
[^3] This MoldMaking Technology article discusses bringing topology optimization to injection molds, which is relevant to mold venting topology optimization.
[^4] This Nature article focuses on multidisciplinary design optimization of lattice-based battery housing for electric vehicles, addressing the inclusion of porosity for weight saving.
[^5] This page from AMT Die Casting describes high integrity die casting, emphasizing the importance of vacuum in achieving high-integrity components.
[^6] This PDF document from Die Engineering provides a manual for vacuum valves, including information on their placement and maintenance in die casting processes.