How Can Die Casting Companies Cut Costs with Aluminum Recycling and Energy-Efficient Systems?
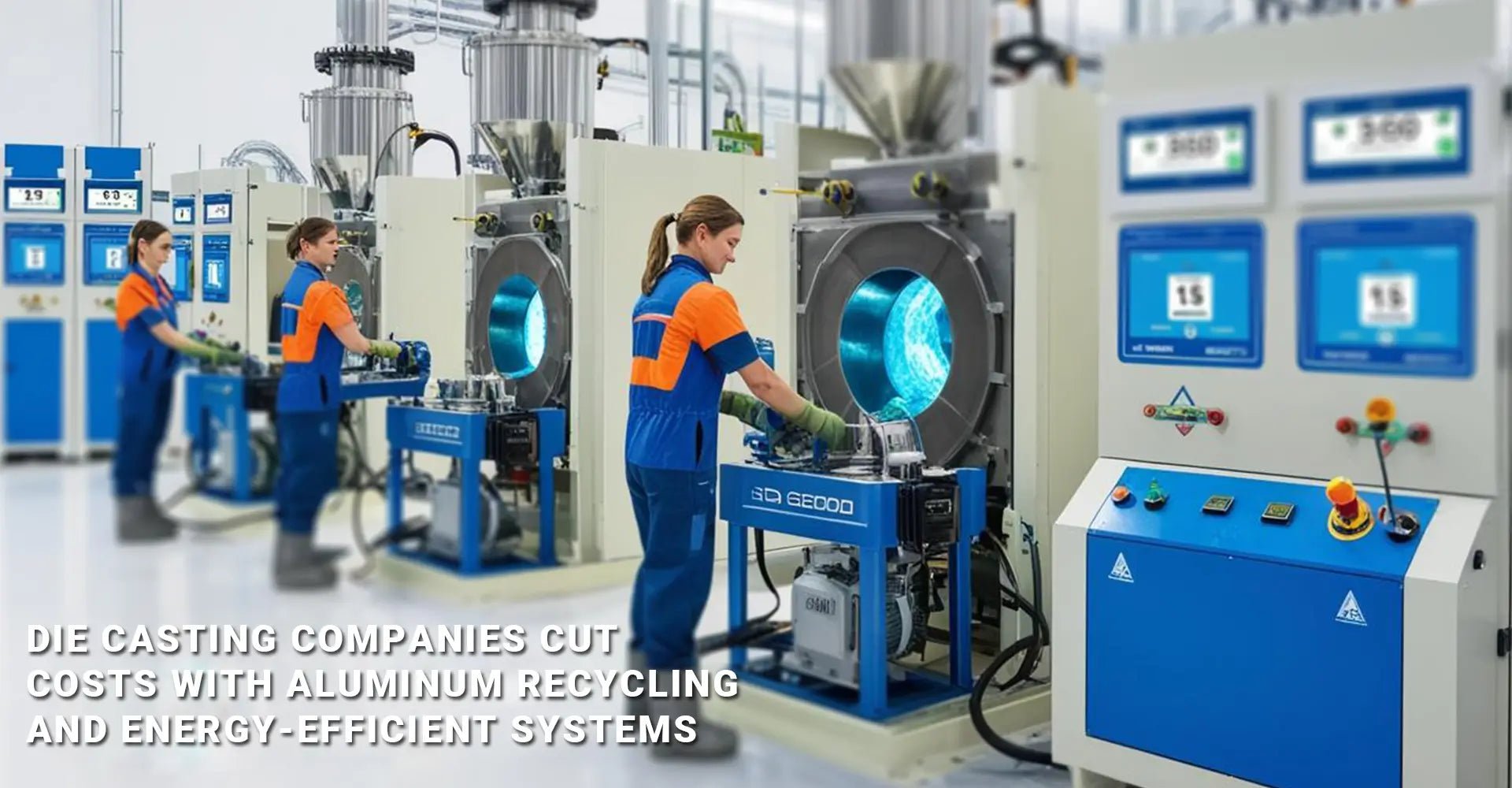
How Can Die Casting Companies Cut Costs with Aluminum Recycling and Energy-Efficient Systems?
In today's competitive manufacturing landscape, die casting companies face mounting pressure to balance economic viability with environmental responsibility. Implementing sustainable die casting practices isn't just good for the planet—it delivers tangible financial benefits. By embracing closed-loop aluminum scrap remelting for foundries and adopting ISO 50001 energy-efficient die casting machines, manufacturers can significantly reduce operational costs while meeting increasingly stringent environmental regulations. This practical approach transforms sustainability from a corporate social responsibility checkbox into a strategic competitive advantage.
The numbers speak for themselves: Companies implementing aluminum recycling programs consistently report 15-20% cost savings on material procurement. Moreover, recycling aluminum consumes a mere 5% of the energy required for primary production—translating to 95% energy savings. Additionally, for every ton of aluminum recycled instead of produced from raw bauxite, approximately 17 tons of CO₂ emissions are avoided. These impressive figures demonstrate why sustainable manufacturing isn't just environmentally responsible—it's financially smart.
Throughout this article, we'll explore proven strategies for implementing sustainable practices in die casting operations. From establishing closed-loop recycling systems to achieving ISO certification and incorporating cutting-edge technologies, you'll discover practical steps that real-world manufacturers have successfully deployed. Furthermore, we'll examine how these approaches not only reduce environmental impact but also deliver measurable improvements to your bottom line through decreased material costs, lower energy consumption, and enhanced operational efficiency.
Table of Contents
- Why Does Closed-Loop Aluminum Recycling Reduce Material Costs by 15-20%?
- What Steps Are Required for ISO 50001 Certification in Die Casting Operations?
- How Can Die Casting Companies Achieve Zero Landfill Waste?
- What Energy Savings Can Variable Frequency Drives Deliver in Die Casting?
- Conclusion
Why Does Closed-Loop Aluminum Recycling Reduce Material Costs by 15-20%?
Closed-loop aluminum scrap remelting for foundries represents one of the most impactful sustainability initiatives available to die casting operations. This approach captures and processes waste material that would otherwise be sold at scrap value or discarded.
The economic advantage is straightforward yet powerful: recycled aluminum costs approximately $0.80 per pound compared to $1.20 per pound for virgin material. For a mid-sized operation processing 500,000 pounds of aluminum annually, this 40-cent differential translates into $200,000 in potential savings. Additionally, the reduced energy consumption significantly lowers utility bills, creating a dual financial benefit.
When die casting operations implement comprehensive scrap management systems, they recover value from gates, runners, flash, and rejected parts—materials that constitute up to 40% of total aluminum usage in many facilities. Advanced melting technologies now achieve material recovery rates exceeding 95%, dramatically improving upon older systems that suffered from oxidation losses and contamination issues. The aluminum in CNC machining chips and swarf can also be incorporated into this recycling stream, further expanding the benefits across multiple manufacturing processes.
What Steps Are Required for ISO 50001 Certification in Die Casting Operations?
ISO 50001 certification provides a structured framework for implementing energy management systems that systematically improve efficiency. For die casting operations specifically, this certification process requires several strategic steps but delivers substantial return on investment.
The certification journey begins with comprehensive energy audits that identify baseline consumption patterns and opportunities for improvement. Companies must establish Energy Performance Indicators (EnPIs) tailored to die casting processes and implement monitoring systems to track progress. Advanced operations are now incorporating AI-driven process optimization tools that continuously adjust parameters to maximize energy efficiency while maintaining quality standards.
Low-energy die casting equipment certification forms a crucial component of ISO 50001 compliance. This involves evaluating machines against standardized efficiency benchmarks and implementing improvements where necessary. Contrary to common misconceptions, certification doesn't always require complete equipment replacement. Many manufacturers successfully achieve compliance by retrofitting existing machinery with energy-efficient components and updating control systems. The certification process typically takes 6-12 months, with costs ranging from $15,000-$50,000 depending on company size and existing energy management infrastructure. However, energy savings typically recover these expenses within 18-24 months, making certification a sound financial decision for forward-thinking die casting operations.
How Can Die Casting Companies Achieve Zero Landfill Waste?
The concept of zero-waste aluminum remelting technology represents the gold standard in sustainable manufacturing. Progressive die casting operations are demonstrating that eliminating landfill waste isn't just an aspirational goal—it's an achievable reality with existing technology.
A standout case study comes from a U.S. foundry that reduced virgin aluminum use by 40% through implementing closed-loop shredding and advanced extrusion processes. This facility invested $1.2 million in a comprehensive system that processes all aluminum waste—including difficult-to-handle materials like oily swarf and contaminated scrap. The payback period? Just 16 months, with ongoing annual savings exceeding $900,000.
The ShAPE™ process for high-purity recycled aluminum represents a breakthrough technology in this space. This innovative approach uses Shear-Assisted Processing and Extrusion to refine recycled aluminum, controlling iron impurities below 0.2%—a critical threshold for maintaining material properties. Die casting operations implementing this technology can now produce components from 100% recycled material that achieve 6061-T6 alloy properties with 290 MPa yield strength, matching the performance of virgin material. This capability is particularly valuable for surface finish quality, as recycled material processed through advanced filtration systems now achieves aesthetic standards previously possible only with primary aluminum.
What Energy Savings Can Variable Frequency Drives Deliver in Die Casting?
Variable Frequency Drive (VFD) technology represents one of the most accessible and high-impact energy efficiency upgrades available for die casting operations. These systems dynamically adjust motor speed to match process requirements, eliminating the energy waste inherent in constant-speed motors.
The energy savings potential is remarkable: die casting operations typically report 51% energy reduction when operating motors at 80% load using VFDs compared to traditional motor controls. For a facility with twenty 50-horsepower motors, this can translate to annual savings exceeding $60,000 in electricity costs. Moreover, VFDs reduce mechanical stress during startups, extending equipment life and reducing maintenance costs.
Implementing VFDs contributes significantly to carbon footprint reduction in die casting operations. A typical mid-sized facility can reduce CO₂ emissions by 300-500 tons annually through comprehensive VFD implementation—equivalent to removing 60-100 cars from the road. This technology pairs particularly well with the energy demands of industrial machinery used in die casting, where large motors and hydraulic systems represent major consumption points. Implementation costs range from $3,000-$10,000 per motor depending on size and application, with ROI periods typically between 8-14 months based on usage patterns and local energy costs.
Conclusion
Implementing sustainable die casting practices delivers compelling financial and environmental advantages for forward-thinking manufacturers. By adopting closed-loop aluminum recycling, pursuing ISO 50001 certification, implementing zero-waste technologies, and upgrading to energy-efficient systems, companies can reduce costs while strengthening their competitive position.
The data clearly supports the business case: 15-20% material cost reduction through recycling, 95% energy savings compared to virgin aluminum production, and potential energy consumption reductions of over 50% with modern control systems. These improvements directly impact profitability while simultaneously reducing environmental impact—a true win-win scenario in today's manufacturing landscape.
External Links Recommendation
[Sustainable die casting practices][^1]
[Closed-loop aluminum scrap remelting for foundries][^2]
[ISO 50001 energy-efficient die casting machines][^3]
---
[^1]: Discover innovative sustainable practices in die casting that can help your business reduce its carbon footprint and improve profitability.
[^2]: Explore this link to understand how closed-loop systems enhance sustainability and efficiency in foundries, reducing waste and costs.
[^3]: Learn about ISO 50001 standards and their impact on energy efficiency in die casting, which can lead to significant cost savings and environmental benefits.
-
Posted in
aluminum die casting